Что такое 5S? Система 5S. Система 5с
Что такое система 5S
Система 5S – это система организации рабочего места, которая позволяет значительно повысить эффективность и управляемость операционной зоны, улучшить корпоративную культуру, повысить производительность труда и сохранить время. Это первый шаг на пути к созданию бережливого предприятия и применению других инструментов системы менеджмента компании Toyota.
Краткая история системы 5S
В Японии системный подход к организации, наведению порядка и уборке рабочего места возник в послевоенный период, точнее, к середине 50-х годов ХХ века. В то время японские предприятия были вынуждены работать в условиях дефицита ресурсов. Поэтому они разработали для своего производства метод, при котором учитывалось все и не было места никаким потерям.
Первоначально в японской системе было только 4 действия. Слова, обозначающие эти действия, в японском языке начинаются с буквы «S»:
- Seiri (整理)– Sorting –
- Seiton (整頓) – Straighten or Set in Order –рациональноерасположение.
- Seiso (清掃) – Sweeping – уборка.
- Seiketsu (清潔) – Standardizing – стандартизация работ.
Позже добавилось пятое действие, его назвали Shitsuke (躾) – Sustaining – поддержание достигнутого и совершенствование, и оно завершило цепочку элементов, которые теперь известны как 5S.
Сейчас система 5S обладает фундаментальной мощью для того, чтобы изменять рабочие места и вовлекать в процесс улучшений всех работников.
В систему 5s входят пять действий:
1) Сортировка
Рабочие и руководители часто не имеют привычки избавляться от предметов, которые больше не нужны для работы, сохраняя их поблизости «на всякий пожарный случай». Обычно это приводит к недопустимому беспорядку или к созданию препятствий для перемещения в рабочей зоне. Удаление ненужных предметов и наведение порядка на рабочем месте улучшает культуру и безопасность труда. Чтобы более наглядно продемонстрировать, сколько лишнего скопилось на рабочем месте, можно на каждый предмет-кандидат на удаление из рабочей зоны повесить красный ярлык (флажок).
Все сотрудники вовлекаются в сортировку и выявление предметов, которые:
- должны быть немедленно вынесены, выброшены, утилизированы;
- должны быть перемещены в более подходящее место для хранения;
- должны быть оставлены и для них должны быть созданы и обозначены свои места.
Необходимо чётко обозначить «зону красных ярлыков» предметов с красными флажками и тщательно её контролировать. Предметы, остающиеся нетронутыми свыше 30 дней, подлежат переработке, продаже или удалению.
2) Рациональное расположение – означает определить и обозначить «дом» для каждого предмета, необходимого в рабочей зоне. Иначе, если, например, производство организовано по сменам, рабочие разных смен будут класть инструменты, документацию и комплектующие в разные места.
3) Уборка (содержание в чистоте) – значит обеспечить оборудованию и рабочему месту опрятность, достаточную для проведения контроля, и постоянно поддерживать её.
Уборка в начале и/или в конце каждой смены обеспечивает немедленное определение потенциальных проблем, которые могут приостановить работу или даже привести к остановке всего участка, цеха или завода.
4) Стандартизация – это метод, при помощи которого можно добиться стабильности при выполнении процедур первых трех этапов 5S – значит разработать такой контрольный лист, который всем понятен и прост в использовании. Продумать необходимые стандарты чистоты оборудования и рабочих мест, и каждый в организации должен знать, как это важно для общего успеха.
5) Совершенствование
Мероприятия, лежащие в основе 5S (сортировка, рациональное расположение, уборка, стандартизация и совершенствование), абсолютно логичны. Они представляют собой базовые правила управления любым продуктивно работающим отделом. Однако именно системный подход, который система 5S применяет к этим мероприятиям, и делает ее уникальной.
См. также:
Что такое 5S. Система 5S. Система 5с
Поделиться в соц. сетях
Система 5S — эффективная организация рабочего места
Большинство сотрудников офисов, предпринимателей, бизнесменов и огромное количество других специалистов сегодня проводят большую часть дня за рабочим столом. Его организация очень важна для продуктивности сотрудника, потому что беспорядок или неправильная расстановка канцелярского оборудования помогает повысить функционал и эффективность работы. В этом вам поможет японская система организации рабочего места 5S.
Что такое система 5S и как ее используют?
Япония сегодня считается одной из самых развитых стран, которая имеет уникальную систему управления внутри компании, а также высокоэффективные производства. Но только по окончанию Второй мировой войны экономика Японии была в ужасном состоянии, потому что множество государств перестали с ней сотрудничать, промышленное производство было уничтожено, рабочих кадров очень мало, а сама страна была в долгах. Кроме того, существовали проблемы безработицы и дефицита товаров, поэтому жители страны начали требовать реформ и перемен.
Одним из таких предприятий, который уже находились на грани разорения, была компания Toyota. В этот период объемы сборки товаров упали до минимума, а количество сотрудников сократилось почти вдвое. И все изменилось практически за несколько лет, когда фирма начала зарабатывать несколько миллионов в год. Сегодня историю успеха Toyota ставят в пример другим корпорациям, которые начинают терять прибыль.
Первое, что сделали руководители и владельцы Toyota – изменили систему работы и разработали совершенно новые принципы. Именно благодаря им предприятие стало одним из самых успешных и крупных производителей автотехники в мире.
Один из новых механизмов, которые используются в Toyota, является методика организации рабочего процесса – это философия бережливого производства. Менеджеры этой компании выдали несколько книг и провели крупное исследование, после чего огромное количество других компаний тоже начали запускать такую же систему на своей фирме. В Toyota даже открыли специальный отдел, который занимался консалтинговыми услугами, чтобы помочь правильно организовать работу в других предприятиях. Кроме того, руководители отделов могут самостоятельно ознакомится с функционалом прямо в Toyota.
Владельцы компании утверждают, что они не создавали намеренно определенные принципы. Просто тогдашние руководители пытались срочно поменять систему производства, в результате чего появилась такая система. Из-за этого многие фирмы, которые пытаются наследовать механизм, не достигают таких успехов.
5 правил организации рабочего пространства
Основной сутью японской системы 5S является пять правил, которые используются владельцами рабочего стола. Весь механизм работы бережливого производства зависит от того, что каждый сотрудник прикладывает усилия для работы, при этом он реализует свои способности на полную и может сосредоточится именно на рабочем процессе.
5S состоит из пяти этапов.
Сортировка.
На рабочем столе размещается огромное количество предметов. Часто они могут быть незначительными или слишком маленькими и владельцу может казаться, что на самом деле со столом все в порядке. По сути предметы можно разделить на три категории:
- Необходимые – это те предметы, которые обязательно должны быть на вашем столе. Их нужно размещать под руками, чтобы быстро дотянуться.
- Нужны периодически – время от времени они могут понадобиться, но большую часть дня вам не нужно пользоваться этими вещами.
- Ненужные предметы – это те вещи, которыми вы вообще не пользуетесь, и они неизвестно как попали на ваш стол. Естественно, эту категорию нужно убрать из рабочего стола.
Соблюдение порядка.
После того, как вы убрали лишнее, нужно рассортировать то, что осталось. Более важные предметы должны располагаться так, чтобы вы не тратили время на поиск и могли на уровне рефлексов достать изделие.
Можете воспользоваться такими правилами, которые предлагают в Японии:
- Необходимые предметы лежат на видном месте.
- Нужные вещи лежат так, чтобы вы могли достать их рукой, при этом не поднимаясь с места.
- Предметы, которые используются постоянно, не берутся в руки тоже должны быть размещены так, чтобы в естественном положении их можно применять. Имеется в виду, например, клавиатура и мышка компьютера. Вы садитесь за стол и кладете руки так, чтобы они сразу легли на мышку и клавиатуру.
- В течение дня после использования нужные предметы должны ставиться обратно на свое место.
Содержание в чистоте.
Японцы советуют разбить рабочее место на несколько зон, каждая из которых будет отвечать за определенные изделия. Например, центр стола – для ноутбука или компьютера; левая часть – для канцелярии; правая – для документов.
Стандартизация.
Чтобы такие принципы производства были действительно полезными и эффективными для всего предприятия, нужно ввести их как стандарт. Абсолютно все сотрудники должны этого придерживаться, как и того, что на работу нужно приходить в 9 часов утра.
Лучшим вариантом будет сделать специальный документ, с которым ознакомятся все сотрудники. После этого периодически можно проверять результаты. Кроме того, нужно прояснить причину такого строгого контроля.
Совершенствование.
Любое действие и особенности поведения человека можно сделать привычкой. Конечным этапом 5S является доведение всех правил до того, чтобы они выполнялись на автоматизме.
Если раздумывать над правилами поведения и организации рабочего места, то по сути Toyota не придумала ничего нового. Но если их придерживаться, то можно заметить этот результат. Кроме того, самодисциплина на рабочем столе повышает производительность и в обычной работе.
Кол-во просмотров: 14 474
Ничего лишнего. Организация рабочего места по системе 5S | GeekBrains
Японский способ навести и поддерживать порядок на столе и в жизни.
https://gbcdn.mrgcdn.ru/uploads/post/1932/og_image/1203efd47116d0f552323ea028b97ab5.jpg
5S — это японская система, которая помогает упорядочить ту сферу, в которой она применяется. Считается, что если следовать ей в жизни, это поможет стать немного счастливее. Но это уже продвинутый уровень.
Чтобы проверить, работает ли система, предлагаем начать с малого — организовать рабочий стол по этому принципу. Это должно помочь обнаружить и устранить проблемы трудового процесса и повысить его эффективность.
Неопрятное и захламленное рабочее место вынуждает отвлекаться, подолгу искать нужные вещи. Это злит и мешает чувствовать удовлетворенность от того, чем вы занимаетесь.
В чем суть
Система состоит из пяти этапов, названия каждого из которых начинаются в японском языке на букву «с». При переводе обычно это пытаются сохранить. В этом нет никакого сакрального смысла, но так получается красивее — название 5S сохраняет оригинальное значение.
Итак, вот эти пять элементов:
- Сортировка.
- Соблюдение порядка.
- Сияющая чистота.
- Стандартизация.
- Самодисциплина.
Каждый из них подразумевает действия, которые в итоге должны привести к порядку на столе и облегчить процесс работы.
1. Сортировка
Этап, в котором нет места сантиментам. Все, что лежит на вашем столе и вокруг него, должно быть рассортировано по двум характеристикам — нужное и ненужное. Во вторую группу отправятся и мусор, и бумаги, которые еще вчера были нужны, а сегодня превратились в хлам, и милые сердцу вещицы вроде фигурок «Мстителей» или счастливого евроцента из первого путешествия за границу. Все это стоит выкинуть, отдать нуждающимся, отнести домой или хотя бы подальше от рабочего стола, если работаете на удаленке.
После этого нужно еще раз рассортировать нужное на то, что необходимо часто, и то, что вы используете изредка. А вот что с этим делать — уже в следующем пункте.
2. Сохранение порядка
На вашем рабочем столе остались только необходимые вещи, но и их нужно разложить так, чтобы уже завтра не вернуться к хаосу и завалам. У каждого инструмента должно появиться свое место, которое отвечает нескольким критериям:
- Вещь лежит на видном месте.
- Ее легко взять.
- Ее легко использовать.
- Ее легко вернуть на место.
Чем чаще вы используете предмет, тем тщательнее стоит выбирать место, где он будет лежать. Скажем, если вы каждые десять минут записываете что-то в ежедневник, едва ли есть смысл убирать его в ящик стола. С большой долей вероятности вам быстро надоест доставать его оттуда, и вы просто перестанете возвращать его на место.
Зато блокнот можно пристроить рядом с клавиатурой со стороны нерабочей руки. Смотрите, как просто: вы протягиваете руку, берете ежедневник, подтягиваете к себе, открывая в процессе, и тут же начинаете делать записи рабочей рукой — ни одного лишнего движения.
А вот гарнитура, которую вы используете раз в неделю для интернет-планерки, в ящике стола будет вполне на своем месте.
3. Сияющая чистота
Чтобы рабочий стол оставался чистым, его нужно периодически приводить в порядок. Этому правилу, не апеллируя ко всяким японцам, с детства учат русские мамы. И оно работает.
Проще всего поддерживать чистоту, если определить время для уборки. Это звучит гораздо зануднее, чем есть на самом деле. Например, заведите правило — перед окончанием рабочего дня выкидывать ненужные бумаги в мусорное ведро, лишние файлы — в корзину, а рабочие инструменты возвращать на место. Всего 5 минут, и рабочий стол будет выглядеть так, что и маме показать не стыдно.
4. Стандартизация
5. Совершенствование
Этот этап не закончится никогда, потому что нет предела совершенству. В процессе работы за преобразившимся столом вы начнете понимать, что некоторые решения были неправильными. Внесете коррективы и впредь будете действовать уже с новыми вводными.
Зачем все это нужно
Описание системы выглядит сложно. На практике все гораздо проще. Немного усилий, и вот что вы получаете взамен:
- Чистый стол, на котором не задерживаются лишние вещи. Работать за ним легко и приятно: вы не отвлекаетесь, ничего не мешает.
- Все необходимое под рукой. Вам не нужно искать ту самую важную бумажку. Она лежит с другими не менее важными документами, в установленном вами порядке. Больше не придется тратить время впустую. Рука автоматически тянется к месту, где должен быть нужный предмет, и, что важно, находит его там.
- На рабочем месте легко ориентироваться не только вам. Вы легко объясните по телефону или в чате, что и где лежит, даже человеку, который впервые в глаза видит ваше рабочее место. Вы знаете точные координаты и не используете фразу «ну где-то там, на столе».
Кому подойдет
Всем подойдет, но в особенности тем, у кого много подручных материалов. Если вы используете только ноутбук, теоретически можете поставить его даже на гору мусора. Ничего не помешает — вам нужны только компьютер и клавиатура. Но если потребуются документы, бумаги с записями, макеты, что-то еще, то стол моментально исчезнет под завалами. В таких условиях любой лишний предмет сеет хаос.
А вы как организуете рабочее место? Делитесь в комментариях.
Развитие производственных систем. Система организации рабочего места 5S
1. Развитие производственных систем
© Алцыбеева И.Г, Ганебных Е.В., Гурова Е.С.1.1 Система организации рабочего места 5S
Приобретение нового
оборудования
Приобретение нового
инструмента
Обучение персонала
Рабочее место
3
Система 5S (5С) – это малозатратный
системный подход к управлению
пространством, как физическим, так
и информационным
Зачем нужна 5S?
Почему именно 5S?
Беспорядок приводит к утрате
материальных ценностей
Можно начать применять
СЕГОДНЯ
В беспорядке сложно и долго
искать нужную вещь
Не требует высоких вложений
Хаос на рабочем месте
порождает
неорганизованность
Клиенты формируют мнение
об организации и по внешнему
впечатлению
Дает мгновенные и видимые
результаты
Участие может принять
каждый
5
Беспорядок:
— Вещи складированы так, что при
необходимости взять один
предмет, приходится
перекладывать другие
— Слишком много запасов
— Предметы не подписаны, что
затрудняет их поиск и выбор
— Много ненужных предметов
Основные потери:
— Время на поиски новых предметов
— Порча документов при хранении
— Ненужные движения при
перемещениях от предмета к
предмету
— Излишние запасы – заморозка
оборотных средств
6
Классические этапы системы 5S
7
1 ЭТАП: Сортировка
Все предметы делим:
ВСЕГДА НУЖНЫЕ
ИНОГДА НУЖНЫЕ
НИКОГДА НЕ НУЖНЫЕ
Параллельно составляется список недостающих предметов!
8
7.

• «Красный ярлык» карантинная зона
8. Этап 1: Сортировка
• Нужен ли этот предмет?• Если да, то в каком
количестве?
• Где его лучше разместить?
Еще одно назначение «красного
ярлыка» — поиск востребованности
этого предмета на соседних рабочих
местах.
9. Этап 1: Сортировка
НЕ СОМНЕВАЙТЕСЬ!НЕ ПЕРЕУСЕРДСТВУЙТЕ!
10. Этап 1: Сортировка
Предметы с эмоциональной привязкой2 ЭТАП: Систематизация
Это организация хранения НУЖНЫХ вещей
Простой и быстрый поиск
любой вещи без затруднений
Возврат вещей на место без
лишних вопросов
11
2 ЭТАП: Систематизация
Макроуровень: макропланировка
12
2 ЭТАП: Систематизация
Микроуровень: микропланировка
13
2 ЭТАП: Систематизация
Степень необходимости (частота
использования)
Предметы, которые Вы не
Н
использовали в течение
и
последнего года
з
Предметы, которые Вы
к
использовали только один
а
раз в течение последних 6я
12 месяцев
Решение о хранении
(распределение)
Удалите их
Храните их на известном
расстоянии (отдельный
склад на территории
производства/ АБК)
14
2 ЭТАП: Систематизация
Степень необходимости (частота
использования)
Предметы, которые Вы
С
использовали только один
р
раз в течение последних 2е
6 месяцев
д Предметы, которые Вы
н
используете более одного
я
раза в месяц
я
Решение о хранении
(распределение)
Храните их на среднем
расстоянии (один склад
на территории
цеха/департамента)
Храните их на среднем
расстоянии, недалеко от
рабочего места (один
склад на участке/ в
отделе)
15
2 ЭТАП: Систематизация
Степень необходимости (частота
использования)
В
ы
с
о
к
а
я
Предметы,
используемые один раз в
неделю
Предметы,
используемые
ежедневно
Предметы,
используемые ежечасно
Решение о хранении
(распределение)
Храните вблизи
рабочего места
Храните на рабочем
месте или носите с
собой
16
2 ЭТАП: Систематизация
83% информации – зрение
11% информации – слух
3,5% — обоняние
1,5% — тактильно
1% — вкус
2 ЭТАП: Систематизация
Какой цифры здесь не хватает?
18
2 ЭТАП: Систематизация
А в этой таблице?
19
2 ЭТАП: Систематизация
Обеспечить визуальную доступность и легкий поиск
20
2 ЭТАП: Систематизация
Систематизация:
сократит время на
выполнение
операций
увеличит
производительность
внесет строгую
последовательность,
которая позволит
избежать хаоса на
рабочем месте
21
3 ЭТАП: Содержание в чистоте
Определите объекты для регулярной уборки
Установите периодичность уборки – выделите
время и установите регламент
Распределите ответственность
Контролируйте
ВАЖНО! ИСКЛЮЧИТЬ ПРИЧИНУ ЗАРЯЗНЕНИЯ!
22
3 ЭТАП: Содержание в чистоте
Эффекты данного этапа:
появление удовлетворенности работника своим рабочим
местом
полная готовность предметов, которые нужны для
выполнения работы
повышается безопасность рабочего места
постоянный осмотр во время уборки помогает выявить
проблемы
23
4 ЭТАП: Стандартизация
• Стандарт – это способ закрепить уже
достигнутые улучшения, прежде чем
перейти к разработке новых
24
Стандарт 5S
25
4 ЭТАП: Стандартизация
26
4 ЭТАП: Стандартизация
• Стандарт по сортировке
27
4 ЭТАП: Стандартизация
• Стандарт по содержанию в чистоте
28
29
30
30
30
4 ЭТАП: Стандартизация
Эффекты данного этапа:
позволяют в будущем поддерживать
результат, достигнутый по окончании 5
шагов
в случае отсутствия основного работника
любой коллега в случае необходимости
сможет найти информацию/документ на
его рабочем месте, в компьютере,
эффективно заменить его
31
5 ЭТАП: Соблюдение и
совершенствование
• Важно, чтобы все (от
самого высшего
руководства и до самого
рядового работника)
осознали систему 5S как
общепринятую философию
повседневной
деятельности
32
5 ЭТАП: Соблюдение и
совершенствование
• Чек-лист аудита соблюдения системы 5S
33
36.

37. 1 этап — сортировка
38. 1 этап — сортировка
Типы «мусорных» файлов:1 этап — сортировка
• Отпишитесь от ненужных рассылок
• Уберите ненужные программы из
автозагрузки компьютера
• Используйте клавиатуру без
клавиш Sleep, Wake, Power
• Не храните свои документы на
диске С
40. 2 этап — систематизация
Поставьте обновление электронной почты не чаще, чем раз в 30
минут, чтобы увеличить интервалы работы в режиме погруженности в
процесс.
Попросите своих коллег все несрочные вопросы направлять по
электронной почте, а не задавать их по телефону.
Создайте четкую структуру папок на своем компьютере и правильно
проименуйте нужные файлы. Создайте удобную систему, которой
будете придерживаться на автоматизме.
Проанализируйте, к каким папкам вы чаще всего преодолеваете
длинный путь и выведите их ярлыки на рабочий стол.
Для устранения эффекта набора текста на противоположной
раскладке клавиатуры ghbvthyj nfrbv j,hfpjv, установить программу
(например, Punto Switcher) .
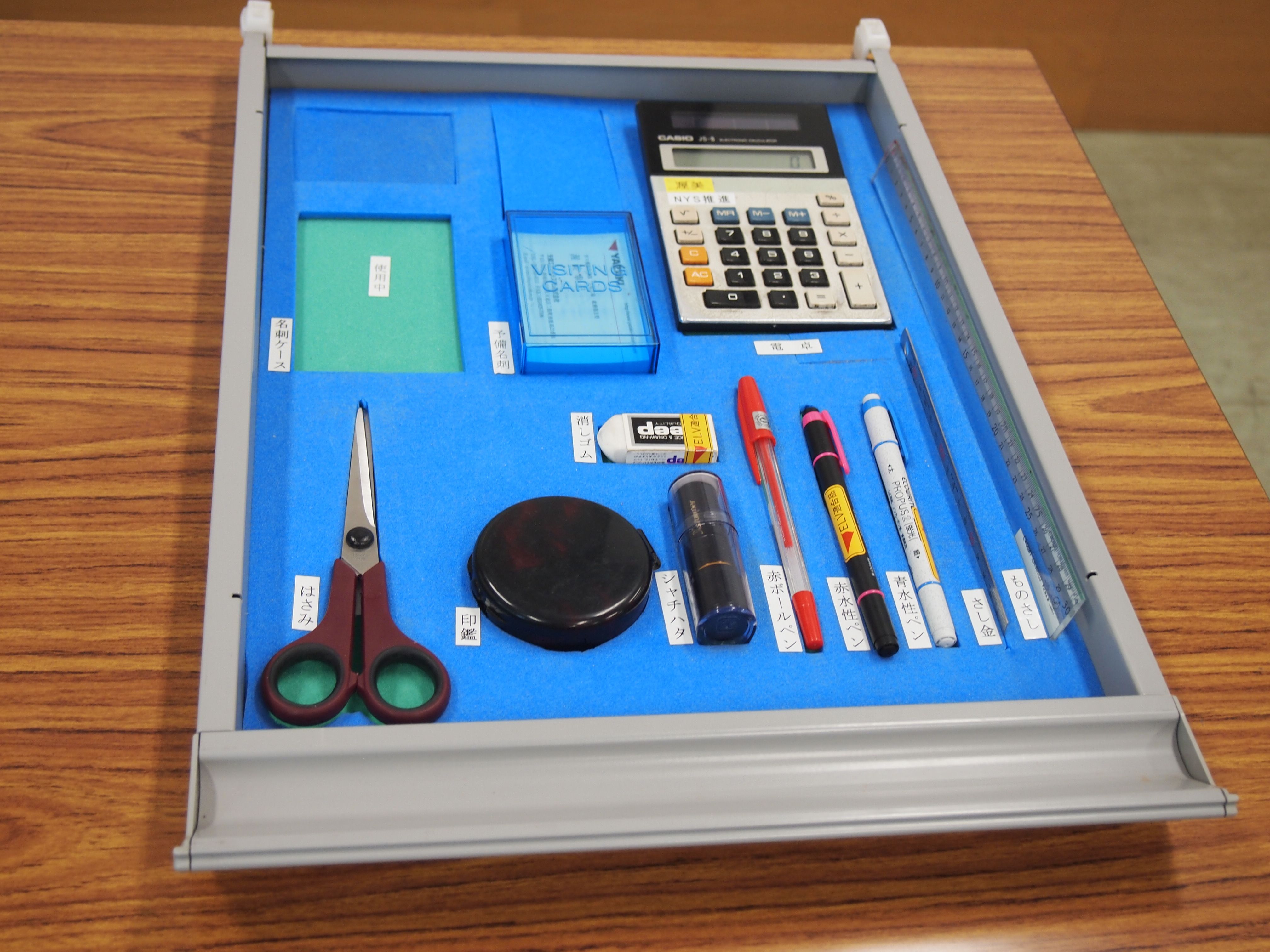
41. 2 этап — систематизация
• Калькулятор выведите в горячие клавиши или используйте программы(например, NumLock Calculator).
• Если у вас ноутбук, и на нем ваша скорость набора текста падает из-за
неудобной клавиатуры – не стесняйтесь и подключите внешнюю
клавиатуру через USB
• Компьютерную мышь можно использовать с дополнительными
клавишами по бокам, и дополнительную клавишу под большой палец
запрограммировать, например, под действие «Назад», что ускорит
ваш серфинг по папкам. Зашли в папку – не то. Не надо тянуться к
кнопке проводника «Назад», просто мгновенно нажимаете большим
пальцем дополнительную клавишу мыши и смотрите следующую
папку.
• Добавьте в автозагрузку те программы, которые сразу запускаете в
начале каждого рабочего дня.
42. 3 этап – содержание в чистоте
• Проводите чистку системы специализированными программами.• Проводите дефрагментацию системного диска.
• Процесс очистки клавиатуры с помощью салфеток может быть очень
длительным и трудоемким.
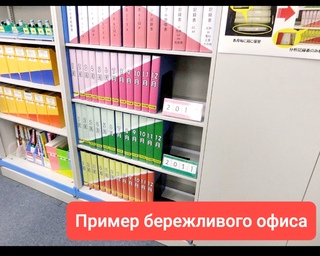
верхнюю панель клавиатуры, поместить ее под струю воды из под
крана, почистить щеткой для одежды с хозяйственным мылом,
стряхнуть воду, дать немного просохнуть и собрать клавиатуру. Чистота
– идеальная, а также вы избавляетесь от всего, что накопилось не
только на клавишах, но и под ними.
• Внутри системного блока может скапливаться много пыли, это ведет к
перегреву вследствие замедления вращения вентиляторов, «эффекта
одеяла», задерживающего тепло элементов, покрытых толстым слоем
пыли. С этой проблемой лучше справляться с помощью пылесоса.
43. 4 этап – стандартизация
Идеальный вариант – сетевое хранилище файлов с общимдоступом:
01_Справочная информация
02_Проекты
03_Бланки отдела кадров
04_Сметы и калькуляции
Прописывайте в имени файла его версию, дату и автора,
например «План перестановки цеха вер.2.4 Сидоров»
• Полюбите процесс оптимизации!
• Не бойтесь пробовать!
• Ищите варианты оптимизации с азартом и вдохновением
• Оказавшись у чужого рабочего места – осмотритесь, какие
полезные идеи вы можете взять себе
• Испытали, не понравилось, вернули как было!
Понравилось – оставили!
• Распространите идею 5S в компьютере на свой кабинет,
затем на свой отдел и дальше.

новыми наработками, сразу запускайте их в жизнь!
В целом значение системы 5S означает:
40
1.2 Визуальное управление и контроль
41
Информация должна быть проста
для понимания и восприниматься
за один взгляд, мгновенно
42
• Цветовое восприятие:
ЖЕЛТЫЙ СИНИЙ ЗЕЛЕНЫЙ ЧЕРНЫЙ
КОРИЧНЕВЫЙ КРАСНЫЙ СИНИЙ
ЧЕРНЫЙ ЖЕЛТЫЙ ЗЕЛЕНЫЙ
РОЗОВЫЙ СИРЕНЕВЫЙ ОРАНЖЕВЫЙ
КРАСНЫЙ ЖЕЛТЫЙ ЧЕРНЫЙ СЕРЫЙ
43
50. Сигнальная разметка и зонирование
4551. Сигнальная разметка и зонирование
Указатели, таблички46
52. Бамперы безопасности
4753. Визуализация хранения
5054. Визуализация хранения
5155. Визуализация хранения
5256. Визуализация управления
5457. Визуализация управления
Цель визуализации – удобство зрительного восприятия и анализа54
58. 1.3. Стандартизированная работа
9059. Область применения стандартизации
9196
61.

62. Преимущества стандартизации
Для руководителей (мастеров)Для исполнителей
98
Читать онлайн «5S. Организация рабочих мест» — автор Филипп Семенычев
Что такое 5S?
Вначале разберём, что обозначает известная всем аббревиатура, как ее понимать, в чем заключается суть этого метода.
5S — это аббревиатура пяти японских слов, обозначающие порядок улучшения любого рабочего места и его организации. Далее эта аббревиатура была переведена на английский язык, на котором она также очень гармонично легла на 5S — все пять шагов также начинались с «S». После аббревиатура была переведена на русский язык, и в русском языке также нашлись аналоги, начинающиеся с буквы с.
С момента основания бережливого производства 5S считается наиболее распространенным и фундаментальным методом, с которого начинается реализация каких-то улучшений и шагов в направлении бережливого производства.
5S помогает стабилизировать процесс, организовать рабочие места, повысить лояльность персонала, дать понять коллективу, что улучшения, в первую очередь, начинаются на рабочих местах. Метод помогает вовлечь персонал. В настоящее время о 5S написано достаточно много книг, статей, этот метод по праву является наиболее популярным методом в России.
Первый шаг — это сортировка (SEIRI). Четкое разделение предметов на нужные и ненужные и избавление от последних. Избавление от хлама, сломанных, неиспользуемых предметов и так далее.
Второй шаг — соблюдение порядка (SEITON). Организация хранения необходимых вещей и предметов, которая позволяет более быстро и просто найти то, что используется ежедневно. Эти вещи находятся под рукой. То, что используется редко — находится где-то на определенном расстоянии (в шкафу, на складе и т.д.)
Третий шаг — содержание рабочего места в чистоте и опрятности (SEISO). Это поддержание чистоты и устранение источников загрязнения, постоянная уборка. Это то, что поднимает моральный дух и придает рабочему месту красивый, эстетичный и пригодный для работы вид.
Четвертый шаг — стандартизация (SEIKETSU). Это необходимое условие для выполнения первых трех правил. Это закрепление первых трех шагов, документальное либо визуальное. Оно необходимо для улучшения контроля и формирования базы, для выработки привычки.
Пятый шаг — совершенствование (SHITSUKE). Улучшение организации рабочего места, постоянное повторение первых четырех шагов, выработка привычки улучшать рабочее место и повторять первые четыре шага.
Цели и задачи 5S
Следующими важными вопросами являются цели и задачи 5S. Зачем нам нужно 5S? Какой результат можно получить с помощью рациональной организации рабочих мест? Какие задачи можно попутно решать и какие основные цели преследуют эти 5 шагов?
Во-первых, 5S — это система рациональной организации рабочих мест. Вы спросите, зачем нужно рационально организовывать рабочие места, ведь люди и так работают нормально, продукция производится, какая-то прибыль приходит в организацию? Если вы начинаете работу в направлении бережливого производства, система 5S как раз будет являться частичкой фундамента, который позволит применять более сложные комплексные методы и инструменты бережливого производства.
Первая цель, которую преследует система рациональной организации рабочих мест — это стабилизация процессов.
Основная и главная цель заключается именно в стабилизации процессов. Стабильность выражается в способности повторять результат, то есть выдавать определенное количество и качество продукта, которое можно предсказать. Зависит стабильность от различных факторов.
Например, от работы оборудования, качества, технологии, материалов, инструментов, человека, от риска получения травмы, то есть от множества факторов.
И рациональная организация рабочего места как раз устраняет основные потери на рабочем месте, позволяет исключить или уменьшить некоторые факторы, влияющие на стабильность процесса.
Например, когда человек меньше ищет инструмент, быстрее обнаруживает отклонения, когда оборудование более чистое, а рабочее место более аккуратное, то результат, выдаваемый процессом, становится лучше и стабильнее.
Результат может быть стабильно плохим и стабильно хорошим, но, тем не менее, он будет предсказуем, повторяем, и его уже можно будет прогнозировать.
Вторая большая цель рациональной организации рабочих мест заключается в вовлечении и подготовки персонала к более серьезному улучшению.
Организация рабочих мест — это в первую очередь видимые улучшения, которые затрагивают непосредственно рабочих, их рабочие места и операции, то есть там, где человек, который создает ценность, непосредственно работает.
Во время кампании по организации рабочих мест выявляются лидеры. Это неравнодушные к судьбе компании люди, которым важна их окружающая среда, рабочие места и процессы. Персонал начинает поддерживать инициативу руководителя. Он видит, что от простых инструментов, от инициатив руководства в первую очередь для них появляется какая-то польза в виде чистого, опрятного, рационально организованного рабочего места. Работники начинают вовлекаться в сам процесс улучшений, и помочь этому можете вы, начав с того, что организуете рабочие места, сделаете их чистыми, аккуратными, опрятными, рационально выполненными.
Из дополнительных преимуществ, которые влечет за собой применение 5S, можно выделить снижение числа несчастных случаев. Это происходит, если человек меньше спотыкается, когда снижается вероятность того, что что-то может упасть, обо что-то он может ушибиться и так далее. За счет исключения этих травмоопасных ситуаций, связанных с нерациональной организацией рабочего места, снижается число несчастных случаев. То есть повышается уверенность человека в безопасности. Это дополнительное преимущество влечет за собой и вовлечение персонала, и стабилизацию процесса. Это следствие двух основных целей.
Следующее преимущество — повышение качества продукции, снижение количества дефектов. Когда рабочее место и оборудование более чистое, а все предметы рационально расположены, каждый сможет заметить отклонение быстрее, чем обычно, следовательно, и среагировать на брак раньше. Любой может заметить какие-то ошибки в процессе, которые могут повлечь возникновение брака. Самый банальный пример — это то, что в куче различных предметов, среди инструментов и так далее проще затеряться браку, его просто не видно. Как вы понимаете, существует косвенная связь между организацией рабочего места и уровнем качества продукции, в некоторых спецификах процесса прослеживается и прямая связь. Например, в пищевой промышленности, где малейшая грязь или посторонний предмет — это брак продукции.
Очередное преимущество — это создание комфортного психологического климата, стимулирование желания работать. Оно больше относится к механизму вовлечения. Человек привыкает ко всему: к хорошему рабочему месту или к плохому, грязному, неорганизованному. Но когда кампания улучшения рабочих мест (5S) происходит постоянно, это создает такой комфортный психологический климат и стимулирует желание работать у людей. Они видят, что руководство о них заботится. Это влечет за собой дополнительные преимущества: человек чувствует себя в большей безопасности, его работа становится более стабильной, то есть он не дергается на поиск инструмента, не спотыкается, не очищает, например, инструмент от грязи, ему проще фокусироваться на своей конкретной работе по созданию ценности, что повышает удовлетворенность самого работника.
Последнее дополнительное преимущество, которое можно выделить, — это повышение производительности труда, что, в свою очередь, ведет к повышению прибыли предприятия, соответственно, и к повышению уровня дохода рабочих. Повышение производительности труда дает устранение мелких потерь. Перемещение, передвижение, поиск, упаковка и распаковка, перекладывание лишних предметов и т. д. Это всё, чего можно избежать, если убрать с рабочего места все лишнее и оставить только то, что нужно.
Что мы получаем в результате, когда занимаемся организацией рабочих мест? Это чистое и безопасное рабочее место. Это минимальное количество потерь на рабочем месте. Это лояльный персонал, который готов к новым улучшениям. Более стабильные показатели качества и производительности.
Необходимость внедрения 5S обоснована необходимостью иметь стабильное производство в первую очередь. К тому же, полученные в результате компанией чистые и организованные рабочие места являются основой для дальнейших улучшений.
Взаимосвязь организации рабочих мест с потерями
Продолжая исследовать вопрос о необходимости организации рабочих мест, разберёмся во взаимосвязи организации рабочих мест с потерями и в следствиях их наличия. Посмотрим, какие потери есть на рабочих местах и как рациональная организация рабочего места может повлиять на наличие этих потерь и на их количество.
Нерациональная организация рабочих мест является причиной наличия многих потерь на рабочих местах. Это уже понятно, это мы принимаем, как аксиому.
Что же мы можем наблюдать на нерационально организованных рабочих местах?
Можно заметить, что на нерационально организованных местах отсутствует управление процессом, то есть не видны отклонения, проблемы, состояние процесса неясно. Когда на рабочем месте бардак, мы не можем понять, хорошо идет работа или плохо, выполняется ли план, соблюдаются ли нормы качества. Мы видим бардак, при котором мы не можем с помощью каких-то визуальных ориентиров понять, как идёт работа. Нам остается либо досконально разбираться в процессе, спрашивать и искать какие-то подтверждения, либо прибегать к каким-то другим административным средствам.
Мы можем увидеть на нерационально организованных рабочих местах, что процесс становится замкнутым на человека, затрачивается большое количество времени на работу в определенном процессе и увеличивается вероятность ошибок. Что имеется в виду под закрытым процессом? Типичный пример: кроме дяди Васи, никто не знает, где лежит ключ на 20. Если другой человек придет на это неорганизованное рабочее место, он вряд ли сможет сразу выполнить всю работу, которая от него требуется. Он вряд ли сразу сможет найти инструмент или оснастку, быстро сориентироваться в ситуации и понять, где что находится. Он потратит на это очень большое количество времени, и, скорее всего, совершит огромное количество ошибок. Обычно так и происходит. Эта закрытость процесса, опять же, связана с наличием большого количества потерь на рабочих местах.
Третье, что мы можем наблюдать, — это проблемы с производительностью. Много лишних действий, не выдерживается темп производства, нарушаются правила техники безопасности и технология для того, чтобы обеспечить нужную производительность. Потери производительности вызваны наличием большого количества потерь от перемещения по поиску нужных предметов, от ожидания и многих других факторов. Во многом эффективность работы определяется организованностью рабочих мест и отсутствием семи видов потерь, которые мы можем увидеть на нерационально организованных рабочих местах.
Кроме того, можно увидеть взаимосвязь нерациональной организации рабочих мест и потерь. Взгляните на табличку — сверху вы видите 7 видов потерь — излишние запасы, ожидания, перемещения, переделки, перепроизводство, излишнюю обработку и транспортировку. С левой стороны таблички — столбцы, в них вы можете видеть признаки нерациональной организации рабочих мест.
Вообще здесь можно было проставить галочки в каждую клетку, если смотреть не только прямые взаимосвязи, но и косвенные. Например, тот же мусор, грязь может повлиять на перепроизводство, когда какая-то стадия процесса или операция встанет из-за того, что сломается станок, например, от мусора и грязи. И предыдущая стадия будет производить продукт независимо от того, чего хочет внутренний заказчик.
Если говорить в целом о взаимосвязи потерь с организацией рабочих мест, то можно выявить явную зависимость. Например, выход из строя оборудования может быть из-за загрязнения и попадания мусора, что спровоцирует потерю ожидания. Простой следующей стадии производства может быть из-за поиска, например, материалов, документов, изделий, комплектующих и так далее. Все это может вызвать ожидание.
Дефекты может вызвать загрязнение рабочей поверхности, датчиков, попадание пыли, грязи и так далее. Транспортировку может вызвать скопление лишних изделий, которое будет требовать их постоянную сортировку, перемещение, перекладывание. Перемещение вызывают лишние предметы, которые ограничивают свободу действий, отвлекают внимание, требуют дополнительных перемещений. Перепроизводство и запасы могут быть вызваны беспорядком из-за отсутствия четкого представления о необходимости производства и пополнения, такое тоже может быть. Беспорядочные действия работников, выполнение лишней работы, повышение вероятности несчастных случаев, необходимость дополнительных мер для обеспечения безопасности, все это и многое другое порождается как раз нерациональной организацией рабочих мест. Где-то существуют прямые взаимосвязи, где-то косвенные, но рациональная организация рабочих мест исключает практически все виды потерь, а нерациональная, наоборот, способна порождать все семь видов.
На рабочих местах существует огромное количество потерь, устранение большинства из них начинается как раз с рациональной организации рабочих мест. Не надо прибегать к каким-то сложным комплексным аналитическим инструментам и методам. Не надо создавать какие-то большие технические советы, вкладывать деньги в инвестиции. Займитесь тем, что можно сделать сейчас. Меньше ходить, меньше искать, меньше сортировать, меньше спотыкаться, меньше вытирать руки и так далее.
Теперь вы знаете о прямой взаимосвязи между рациональной организацией рабочих мест и наличием потерь. Рациональная организация рабочих мест влияет практически на все виды потерь. Помните о ней, объясняйте её работникам и коллегам.
Условия применения 5S
В данном разделе речь пойдёт о необходимых базовых условиях применения метода 5S. Давайте посмотрим, где применять 5S, и какая требуется подготовка. Соблюдение приведенных в данном разделе условий применения 5S способно существенно улучшить и ускорить продвижение работ по организации рабочих мест. Поэтому внимательно изучите приведенные условия, сопоставьте их с возможностями вашей организации. Возможно, вы сможете оценить, насколько успешной будет кампания по организации рабочих мест и сможете лучше подготовиться.
В первую очередь, залог успешного применения методики 5S — это вовлечение как рабочего персонала, так и руководящих работников. Это командный метод, никто не должен остаться в стороне. Рабочий, бригадир, мастер, закрепленный технолог, инженер по охране труда и так далее. Те, кого можно вовлечь в эту работу — должны быть вовлечены. Работа по организации рабочего места не должна полностью сваливаться на плечи работника. Но, тем не менее, работник должен быть уверен, что сам организует свое рабочее место, принимает решения самостоятельно. Бывает так, что после проведения обучения руководитель просто взваливает всю работу на того, кто работает на конкретном рабочем месте. Он говорит рабочему: «вот это нужно выкинуть», «это сложи в тумбочку», «подпиши стеллаж», «пронумеруй папки» и так далее. Работник остается один со своей работой, он не понимает, что это и зачем. Чем ему сейчас заниматься — производить продукцию и создавать ценность или организовывать рабочее место? Он не понимает, что вообще происходит — то ли это плохое настроение руководителя, то ли начало большой самостоятельной работы по улучшениям.
С другой стороны, неправильно, когда команда, собранная для организации рабочих мест, начинает организовывать рабочее место, например, во время отсутствия работника. «Ладно, организуем рабочее место без него». Представляете, если кто-то начнет наводить порядок у вас дома, менять местами полки, где хранятся носки с трусами. Вряд ли это кому-то понравится.
Вовлечение не означает, что мы должны полностью слушать работника, — это к тому, что порой степень «замыленности глаза» бывает выражена настолько, что любые перемены ему могут казаться ужасом и глупостью. Здесь командная работа помогает рационально подходить к организации рабочего места. С одной стороны, работник чувствует свою сопричастность к изменениям, ведь впоследствии ему придется повторять шаги 5S уже самостоятельно. Сейчас я говорю только о начальном этапе. С другой стороны, «замыленность глаз» работника может существенно затормозить работу, и здесь как раз понадобится помощь команды.
Если команда вместе с рабочим начинает проходить каждый шаг, например, анализировать нужные и ненужные предметы, то степень «замыленности глаз» работника уменьшается. То есть понятно, если спросить работника, зачем ему 3 ключа на 20, он скажет, что они все нужны потому, что один он может потерять, второй его личный, а третий в карточке записан, на учете. Команда здесь может привести такие аргументы, что рациональнее пользоваться одним ключом. Такой простой пример, но тем не менее командная работа — это первый и самый главный залог успешного применения методики 5S, поэтому подумайте, кого можно подключить. Подумайте, как вовлечь и мотивировать работника. Решите, какие знания дать команде и работнику, чтобы «подстегнуть» их к организации рабочих мест.
Используйте внутренние потребности человека быть причастным к изменениям и коллективу, делающему что-то новое. Можно использовать внутренние потребности человека к творчеству.
Например, предложите работнику помощь в реализации его идей по преобразованию рабочего места, тогда работник может с большей долей вероятности вовлечься.
Очень способствует эффективной организации рабочих мест, когда персоналу демонстрируется заинтересованность руководства. Когда руководителю важно, как обстоят дела по рациональной организации рабочих мест, у его подчиненных создается впечатление, что это не разовая кампания, а что-то действительно стоящее для организации. Поощряйте работников, предлагающих меры по совершенствованию существующих стандартов, сокращению времени и трудоемкости работ. Если работник вам говорит, что можно сделать по-другому, более рационально, то любая идея, пусть даже она не реализуется сразу, должна поощряться. Это необязательно должно быть денежное поощрение, простого «спасибо», хлопка по плечу или пожатия руки будет достаточно.
Кроме этого, объясняйте важность предстоящих изменений. Система 5S, как вы знаете, не требует существенных затрат. Ее успех целиком зависит от общего понимания персоналом возможности проводимых изменений. Если человек понимает свои выгоды, важность тех изменений, которые будут проводиться на рабочих местах с точки зрения его организации и выполнения его операций, вовлекаться ему будет проще. Такой работник будет способствовать изменениям и помогать организации.
Если человек понимает, что он будет меньше ходить и искать инструмент, перекладывать какие-то предметы, за это время он может произвести больше продукции. Соответственно, сможет получить большую зарплату и пораньше уйти домой, либо у него будет время на какую-то рационализаторскую деятельность. Если он будет меньше спотыкаться, соответственно, уменьшится риск получения травм. Вовлеченных работников по организации рабочих мест на каждом предприятии можно найти достаточно много, главное всех собрать, систематизировать при обучении до того, как вы ворветесь на рабочее место работника выкидывать все лишнее. Вот это надо до него донести и дать время, чтобы работник переварил информацию.
5S применяют там, где работают люди, это система организации рабочих мест: постоянных и временных, стационарных и передвижных. Не рекомендую начинать с тех мест, где люди не работают, такие тоже часто бывают. Встречаются, например, в энергетике, объекты, где совершается обход. Начинать нужно с тех мест, где именно сейчас работают люди и где они проводят большую часть рабочего времени.
Не требуйте от работников того, чего сами не можете выполнить.
Не оставляйте работника один на один с его рабочим местом, о чем говорилось выше.
Есть еще несколько моментов, о которых следует помнить. Во-первых, убедитесь, что рабочие места выбраны правильно. Это еще одно условие для правильного начала организации рабочих мест. О выборе пилотного участка подробно рассказывается в одном из следующих разделов. Помните, что внедрение 5S должно устранять потери и улучшать условия труда. Если вы видите чистое рабочее место с минимальным количеством потерь, не начинайте организовывать работу только для того, чтобы подписать карандаш или оконтурить степлер. Включайте голову. Рабочее место должно обладать потенциалом, чтобы потом нельзя было сказать, что трудовые и временные ресурсы были потрачены зря. Прежде чем выбирать рабочее место, изучите раздел, где описываются нюансы по выбору пилотного участка.
Применяйте пропаганду в объяснении важности предстоящей кампании. Обучите персонал, в том числе и руководителей нижнего звена управления, объясните им важность кампании, преимущества, которые затрагивают лично их. Например, снижение бесполезного времени, скорейшее выполнение плана, удобство в работе, гигиена труда, снижение риска получения травмы и так далее. Это очень важно — чтобы люди понимали свою выгоду от организации рабочих мест.
Худший вариант реализации любого улучшения — это когда люди сопротивляются, лучший — когда люди способствуют, помогают, и вам надо стремиться к лучшему. Применение пропаганды, объяснение важности предстоящей кампании способно склонить чашу весов в нужную вам сторону.
Запланируйте ресурсы. Для начала кампании необходимо в первую очередь время на уборку, сортировку, упорядочение и так далее, отсутствие времени приведет к авралам, потере эффективности, демотивации, возможному провалу кампании в целом. Зарезервируйте определенное время, например, в конце смены, на проведение кампании.
Например, выделили пол часа в конце смены и занимаетесь организацией рабочих мест. Собрались, провели сортировку, например, в первый день, второй день — провели упорядочение и так далее. Это также относится к руководителям и к каждому члену команды. Кроме того, продумайте материальные ресурсы: средства уборки. Например, устранение источника загрязнения, средства разработки стандартов или метод визуального контроля. Как правило, работа в команде, привлечение дополнительных людей в команду помогает существенно сэкономить время.
Например, при разработке стандартов и элементов визуального контроля. Элементарный компьютер с принтером, где можно напечатать какой-то перечень, список, подпись какого-то стеллажа, шкафчика и так далее. Член команды, который возьмет на себя эти функции, окажет вам существенную поддержку.
Дополнительно к материальным ресурсам относятся те, которые направлены на устранение источников загрязнения, уборку и так далее. На практике встречается много рабочих мест, в которых переломным моментом при организации рабочих мест является либо замена старого стола, либо покраска оборудования. При планировании стоит подумать о тех ресурсах, которые вы можете перераспределить. Не рекомендую тратить материальные ресурсы, особенно в начале кампании.
Заинтересованность руководителей показывает важность и неизбежность предстоящих изменений. Объявите о кампании, интересуйтесь успешностью хода работ. Если вы — исполнитель, стимулируйте вашего руководителя периодически выходить на рабочее место, показывайте результаты работы. Когда руководитель заинтересован, люди видят, что организация рабочих мест важна в масштабе всей организации, что эти изменения — не разовая акция. Это действительно важная работа, которая продлится достаточно долгое время.
Условия применения 5S на самом деле очень просты. В двух словах — планирование и вовлечение. Используйте это перед началом кампании и ваши шансы на успех увеличатся многократно. Планируйте ваши улучшения, продумывайте ресурсы: временные и материальные. Продумайте участников команды и то, как можно вовлечь каждого участника, в частности, рабочего. Подумайте, как заинтересовать руководителя или как помочь руководителю показать заинтересованность. Эти основные условия способны склонить чашу весов в сторону максимально быстрой организации рабочих мест.
Эффект от применения 5S
Несмотря на то, что 5S — это достаточно простой метод, применяющийся как базовый при работе в направлении бережливого производства, он способен дать реальный эффект. Иногда даже очень большой эффект. В настоящем разделе мы покажем, какой эффект может дать внедрение 5S, как его можно оценить и посчитать.
Для начала определим, какие преимущества есть у каждого шага метода 5S.
На первом шаге уменьшаются затраты времени на поиск необходимого. Если мы меньше ищем и перекладываем предметы, когда мы знаем, где они лежат, когда у нас нет лишнего мусора, который мешает, отвлекает наше внимание — соответственно, уже здесь, на первом шаге, уменьшается время на поиск необходимых предметов.
На втором шаге происходит уменьшение затрат времени на поиск необходимого, сокращаются ошибки из-за применения не того, что нужно. Мы избавились от всего, что нам не нужно и оставили только то, что нужно и в том количестве, которое необходимо, в тех местах, где вещи удобно брать, искать и так далее. Соответственно, мы сокращаем количество ошибок из-за того, что применили что-то неподходящее случаю: материал с истекшим сроком годности, неисправный инструмент и так далее. Также здесь исключаются любые другие несоответствия, например, лишние движения.
На третьем шаге сокращается простой оборудования и количество поломок. Операторы лучше знают оборудование, становится меньше несоответствий и поломок, связанных с грязью и мусором. Третий шаг — это наведение чистоты на рабочем месте. Мы можем увидеть источники загрязнения, в том числе и на оборудовании, если рабочее место там расположено. Таким образом снижается возможность простоя.
На четвертом шаге происходит улучшение контролируемости порядка, а в качестве бонуса — высокий уровень командного духа и производственной культуры. Когда первые три шага реализованы, чтобы закрепить результат, вырабатываются стандарты. Стандартизация позволяет более качественно осуществлять контроль и обнаруживать отклонения от нормального состояния намного быстрее.
Пятый шаг — совершенствование. Улучшение организации рабочего места, повышение ответственности персонала — все преимущества, которые перечислены ранее. Это постоянное повторение первых четырех шагов и выработка привычки.
Основными критериями правильного применения 5S могут являться обеспечение безопасности труда, повышение производительности, улучшение качества продукции, уменьшение простоев оборудования, чистота, порядок на рабочем месте, отсутствие любых предметов, которые не относятся к текущей работе, когда визуально заметны любые отклонения в состоянии рабочего места. Еще один из критериев — это скорость нахождения необходимых предметов и эффективное использование в целом рабочего пространства.
Давайте попробуем оцифровать эти преимущества, для чего решим следующую задачу:
Представьте операцию, и после организации рабочего места время выполнения этой операции уменьшилось, скажем, на минуту. Операция вымышлена, этот пример нужен для того, чтобы вы оценили масштаб небольших улучшений. Операция выполнялась за 10 минут, а стала выполняться за 9. Допустим, мы исключили какие-то сортировки, какие-то движения и транспортировки, человек стал меньше ходить за инструментом, искать что-то, время сократилось на одну минуту. Не так много, но тем не менее.
Представим, что за смену операция выполняется 35 раз (происходит 35 циклов), примерное время смены — 350 минут.
В месяц 22 рабочих дня, в год — 12 рабочих месяцев.
Попробуйте посчитать, насколько эффективным в масштабе года стало это улучшение. Что мы получим в масштабах месяца, в масштабе года, что мы получим в плане экономии времени?
Мы экономим за один цикл одну минуту — вместо 10 цикл занимает 9 минут. Если за операцию высвобождается одна минута — а мы повторяем ее 35 раз — соответственно, в смену освободилось 35 минут.
Что это означает для нас? Мы можем отпустить работника раньше с работы, мы можем найти время для какой-то дополнительной работы, например, по уборке и обслуживанию оборудования или организации рабочих мест, либо можно в это время произвести больше продукции, если это необходимо.
Если 35 минут эти поделить на 9, это будет 3,8 дополнительных циклов. Например, если за каждый цикл выполнения работы сотрудник производил одну единицу продукта, то, соответственно, теперь за смену он сможет произвести на 3 единицы больше. Вроде бы сократили 1 минуту, но на 3,8 штук больше.
Давайте посмотрим в масштабе месяца. 22 рабочих смены, умножаем на 35 минут, получается 770 минут мы высвободили простыми улучшениями организации рабочих мест, сокращая время выполнения операции всего лишь на 1 минуту. 770 минут — это 2,4 смены.
770 разделить на 9 будет 85,5 циклов, то есть на 85 единиц продукта в месяц больше. Либо можно производить больше продукции, либо работать на 2,4 смены больше. Если вы до этого работали сверхурочно, например, то теперь работать сверхурочно необязательно.
Если посмотреть в масштабе года, то 770 минут в месяц умножаем на 12 месяцев, получается 9240 минут экономии. Если это количество минут разделить на 9 — мы получаем 1026,6 циклов, или 29,3 рабочих смен. Если 29,3 разделить на количество дней работы — получается 1,3 месяца мы экономим. При тех же планах, той же загрузке, тех же ритмах работы.
Понятно, что этот пример очень условный и есть много моментов, которые можно оспорить, но тем не менее основная цель этого примера была показать взаимосвязь между маленькими сокращениями потерь на рабочем месте и результатом в масштабе года.
Если учитывать мелкие потери времени на рабочих местах, в масштабе года они способны показать достаточно большие затраты. Если их считать, то вы просто удивитесь, какая экономия может быть. Эта экономия часто не используется при организации рабочих мест: кампания проходит, рабочие места становятся красивее и чище. Но эта экономия, которая получается от этой условной минуты (секунды, метра, километра и т.д.), как правило, не используется.
Если бы вы видели, что с помощью рациональной организации рабочих мест вы высвобождаете такое количество рабочих смен в год, наверняка вы бы перераспределили либо загрузку, либо трудовые ресурсы, либо произвели какие-то улучшения в масштабе года. Здесь, имея такую экономию, вы можете либо производить больше продукта. Например, завершать выполнение месячного плана раньше и переводить людей на какую-то другую работу. Вы можете работать ритмично и загрузить ваших людей выполнением каких-то дополнительных функций, например, связанных с улучшениями рабочих мест, обслуживанием оборудования, уборкой и так далее. Либо вы можете сократить, например, штатную единицу либо уменьшить сверхурочные работы. Здесь вам надо смотреть, что делать с этими цифрами применительно к конкретной организации, к ее специфике.
1 минута, сэкономленная на операции в данном примере, отразилась в 29 смен за год или в 1000 единиц продукции.
Подведем небольшой итог.
Необходимо считать все потери. Когда вы занимаетесь любыми улучшениями, считайте все потери: все перемещения, ожидание. Все, что вы сокращаете и улучшаете надо считать, а потери в натуральном выражении переводить в масштабе года. Для этого необязательно иметь экономическое образование. Это может сделать каждый, если показать пример и объяснить логику расчетов. Что делать с этими цифрами, руководитель нижнего звена управления решения не понимает, однако, имея эти данные, управлять процессом уже гораздо проще.
Потери в масштабе года становятся более видимыми и актуальными, потому что если никто не обратит внимание на 1 минуту в масштабе операций, то все обратят внимание на 29 смен в масштабе года. Это совершенно разные цифры, но, тем не менее, математически они одинаковые. Эффект как раз содержится в мелких потерях. Вы можете искать какие-то крупные возможности для улучшения, использовать сложные аналитические методы и инструменты, но несколько небольших потерь, сокращенных сейчас на рабочем месте, через полгода уже могут дать достаточно большой эффект в плане оздоровления организации. Делайте выводы, что делать конкретно с теми цифрами, которые вы получаете. С ними что-то надо делать, потому что если сэкономленная минута во времени цикла выполнения операции не будет востребована, то впоследствии она просто растворится, и улучшенная операция снова будет выполняться за 10 минут. Улучшение может быть утеряно, если с ним ничего не делать.
Таким образом, считайте потери, не пренебрегайте даже малейшим их сокращением. Организация рабочего места способна высвободить огромные резервы, иногда даже достаточные для того, чтобы существенно поднять производительность, причем всей организации. И учтите, что это все без особых материальных затрат.
Считайте потери.
Переводите потери в масштаб года.
Думайте, что делать с ними дальше.
Эффект от организации рабочих мест есть, его надо только увидеть и посчитать.
В завершение оставим вам задачу. Посмотрите на первый рисунок, расположенный ниже. Попробуйте найти на нём 3 любые цифры, например, 2, 39 и 26. Засеките время, которое это займёт.
Теперь представьте, что вы провели сортировку (удалили лишние цифры), соблюдение порядка (разложили цифры по порядку), содержание в чистоте (удалили загрязнения) и стандартизацию (расположили цифры по порядку в одинаковом формате). Посмотрите на следующий рисунок и попробуйте выполнить задание повторно: найти цифры 2, 39 и 26. Сравните время, которое у вас получилось. В разных случаях, время на поиск цифр увеличивается в 1,5—4 раза. Вот вам простой пример эффекта от 5S.
Применяйте этот пример на практике и помните об изложенных в настоящем разделе правилах.
Первый шаг — Сортировка
Сортировка по-японски — SEIRI — это разделение вещей на нужное и ненужное и избавление от последних. В этом суть шага.
На этом шаге от всех предметов, которыми не пользовались продолжительное время, просто избавляются.
Под предметами здесь и в дальнейших разделах понимается все, что угодно, начиная с инструмента, комплектующих материалов и заканчивая документацией и личными вещами. Это все, что можно найти на рабочем месте: папки, карандаши, ручки, детали, какие-то материалы, перчатки так далее. Типичная ситуация — избавиться от ожиданий, поиска нужных предметов, сортировки ненужных.
Основная цель первого шага — это освободить рабочее пространство от ненужных предметов, материалов, инструментов, деталей, комплектующих, документации и т. д.
Основная задача, которую необходимо выполнить для этого — это отделить все нужное от ненужного, оставить только то, что необходимо в нужном количестве. Для этого следует понимать, что все-таки нужно, а что нет. Нужно понимать, что нам нужно, но не сейчас, что может понадобиться, но не скоро.
Есть очень хорошее правило: если сомневаешься — выбрасывай.
То, чем вы не пользовались, например, в течение последнего года, можно смело выбросить.
Эффективность от выполнения первого шага — это освобождение производственных и офисных площадей, исключение захламленности, возможности рационального размещения нужных предметов. Когда рабочие места захламлены ненужными предметами, то вам не просто тяжело найти то, что используется постоянно и нужно, но и это нужное некуда положить. Также можно получить уменьшение травмоопасных ситуаций, когда вы меньше спотыкаетесь, перекладываете хлам, меньше всего валяется под ногами и так далее. Это одна из подзадач первого шага 5S.
Суть первого шага — анализ всех предметов, которые находятся на рабочем месте и удаление ненужных предметов.
Следует определить, что необходимо для работы. Для этого надо понимать, как выполняется работа, что происходит на конкретном месте, в чем заключается суть выполнения операций. Изучите, какие меры предпринимаются для выполнения операций, какой инструмент, приспособления и оборудование используется для выполнения конкретной операции. После того, как вы поймете, как выполнять работу, вам уже станет понятно, что необходимо для ее выполнения.
Когда команда работает над первым шагом, в самом начале появляются идеи не только по исключению лишнего инструмента, но о замене, например, инструментов, приспособлений на более универсальные, производительные и так далее.
После того, как предметы, которые необходимы для работы, определены, мы рассматриваем рабочее место. Сравниваем, что нам необходимо для работы, и что на рабочем месте содержится по факту. Именно такая последовательность шагов позволяет свежим взглядом взглянуть на само рабочее место. Если вы сразу начнете спрашивать, для чего это, а для чего вот это, как правило, каждый предмет, сломанный, старый, ненужный и неиспользуемый, — будет иметь несколько аргументов, почему он находится на рабочем месте. «На всякий случай», «нет запасного», «если сломается аналог» и так далее. Всегда будет находиться много отговорок. Поэтому лучше сначала определить, что нужно конкретно для работы, а потом уже начинать смотреть, какие предметы есть на рабочем месте, и это поможет избавиться от большего количества ненужных предметов.
Во время осмотра рабочего места вы делите предметы на нужные и ненужные. Нужные вы уже знаете. Ненужным, по умолчанию, считаем все остальное. Промежуточная категория между нужными и ненужными предметами — это те, которые используются на рабочем месте, но не постоянно. Это то, что пригодится, например, раз в неделю, месяц, полгода и т. д. Сразу же избавляйтесь от тех предметов, которые не вызывают сомнения — сломанных, с истекшим сроком годности, дублирующих друг друга. Не тратьте время на размышления — это как раз и есть четвертый шаг. Удаляем все ненужное.
Удаление может происходить разными способами. Часто, когда мы проводим подобные кампании, мы выделяем какую-то зону карантина. Например, на полу, обозначенную мелом, скотчем или ленточными ограждениями. После чего складываем туда все предметы, в которых мы сомневаемся. Что можно выкинуть сразу же — мы стараемся выкидывать сразу. То, в чем сомневаемся — складываем в эту «зону карантина». Туда складывается все, что не нужно или вызывает сомнения, если какой-то предмет вызвал сомнения, кладем туда, если через какое-то время сомнения не развеялись, мы избавляемся от него.
Примерно так может выглядеть «зона карантина». Это может быть тара, сетка, просто пространство на полу или столе.
Как определить, нужный это предмет или нет?
Нужные предметы — это те, которые необходимы на конкретном рабочем месте, чтобы выполнить рабочие операции.
Ненужные предметы — это те, относительно которых у нас возникают сомнений в их нужности. Это, как правило, сломанные предметы. Часто бывает такое, что сломался инструмент, порвалась перчатка в трех местах, но ее хранят. Есть такое свойство человеческого мозга — хранить старые вещи. От сломанных предметов мы стараемся избавиться в первую очередь. Также к ненужным можно отнести предметы с истекшим сроком годности. Порой таких тоже накапливается немало. Если даже дома вы разберете аптечку — вы увидите, сколько таких примеров можно найти у вас. Предметы, требующие ремонта. Если их не отремонтировали в течение полугода или года, то вероятность того, что их отремонтируют и возьмут в работу, ничтожно мала. Сюда еще можно отнести предметы, оставшиеся от работы в прежние периоды. Это инструмент, оснастка или материал, который сейчас уже не нужен. Понятно, что это материальные ценности — и они хранятся на рабочем месте.
Это могут быть полуфабрикаты, фурнитура, лекала в том числе, документация, вплоть до оборудования. Также к ненужному можно отнести посторонние предметы. Тара, личные вещи, мусор, то, что допускается к нахождению в производстве, но не на конкретном рабочем месте. Например, личные вещи должны храниться в определенном месте: в шкафу, в тумбочке и так далее. Также к ненужному можно отнести избыток полуфабрикатов. К ненужному можно отнести готовую продукцию, которую не сдали на склад, лишнюю мебель и многое другое.
Вторая категория очень интересная — это не нужные срочно предметы, которые будут использоваться на рабочем месте, но они используются не каждый день, месяц или неделю. Это могут быть предметы, которые используют раз в полгода-год. Можно выделить отдельную зону и складировать туда все, что не нужно или вызывает сомнение, в том числе и эти предметы. Если все-таки в ходе кампании будет решено, что какой-то предмет нужен, нужно определить возможные места, где хранить эти вещи.
Например, если какой-то материал или инструмент не нужен постоянно, то он должен храниться не на рабочем месте, а на складе. Те инструменты, приспособления, материалы, документы, которые используются каждый день, должны быть под рукой, чтобы можно было их просто увидеть и достать. То, что используется реже, может храниться в сейфе, в другом конце рабочего места, участка, офиса, кабинета и так далее.
Другой вопрос — куда определить эти предметы? Основной принцип, который используется — то, что нужно, находится под рукой, чтобы не тянуться и не искать. То, что не нужно срочно — может находиться чуть подальше. Не обязательно сразу выкидывать, но и захламлять рабочее место такие предметы не должны.
Нужные предметы — это те, которые, как правило, постоянно используются в ходе работы в течение рабочего дня.
Если предмет использовался однократно или никогда, его списывают, утилизируют, изолируют. Возможных направлений утилизации ненужного достаточно много. Можно, например, использовать в качестве сырья, передать в другой цех, участок или отдел. Можно сдать на склад. Можно обменять, утилизировать, сдать в пункт приема металлолома или макулатуры.
Если предмет используют редко (например, раз в полугодие), его можно хранить на складе, если мы говорим о цехе. Если об офисе — можно хранить в архиве либо в общем шкафу. Если предмет используют раз в неделю или чаще — возможно хранение на складе на участке, рядом с рабочим местом. Когда очень часто (раз в день или чаще), то место хранения — это рабочее место сотрудника, которое должно быть оборудовано так, чтобы можно было не тратить время на его поиск.
В идеале любой работник должен на рабочем месте быстро найти предмет, необходимый для его работы. Таким образом, чтобы произвести сортировку, нужно определить границы рабочей зоны, определить перечень нужных предметов, внимательно осмотреть рабочую зону, удалить из нее все ненужное и организовать хранение удаленных предметов, так как это необходимо.
Кампания красных ярлыков
Продолжая тему реализации первого шага, познакомимся с кампанией красных ярлыков.
Этот метод пришел из Японии. Суть метода заключается в том, чтобы при проведении кампании по организации рабочих мест на все ненужные предметы или предметы, в которых участники кампании сомневались, прикреплялись красные ярлыки. Ярлык бросался в глаза, он заставлял задуматься, помогал документировать и сортировать предметы, он давал представление о том, что потом делать с данным конкретным предметом.
Что это дает? Во-первых, это визуализация предметов, не отнесенных к категории «нужное». Во-вторых, документирование наличия ненужных предметов. В отличие от простого подхода, описанного при сортировке, в данном случае, при присвоении предмету красного ярлыка, происходит документирование. Записывается, например, в журнал, блокнот, ведомость и т.п., что был изолирован конкретный предмет в определённом количестве по определённой причине. Эта информация из документации может служить для принятия решения о перераспределении предметов. Например, материалы, инструменты, полуфабрикаты, канцтовары и так далее могут быть востребованы на других рабочих местах. Может быть такое, что их вообще там не хватает. Это позволяет перераспределить предметы и рационально утилизировать, например, сдать в макулатуру или металлолом.
Основные требования к методу — это дополнительная подготовка персонала и наличие системы учета и документирования (журналы либо компьютерная база). Дополнительная подготовка заключается в том, что ярлыки надо разработать, напечатать, кроме того, нужно подготовить персонал, чтобы он понимал, что такая кампания проводится и что данные ярлыки нельзя убирать и выбрасывать.
Основное преимущество состоит в том, что все ненужные и сомнительные предметы бросаются в глаза, когда на них есть ярлык и ни один предмет не останется незамеченным, появляется возможность их перераспределения.
На что обычно их клеят?
Наличие красного ярлыка неизбежно для сломанных, у которых истек срок годности, для требующих ремонта предметов, для деталей, оставшихся от производства продукции, а также для тары, личных вещей, мусора, избытка комплектующих, полуфабрикатов и готовой продукции, которая не сдана на склад, лишней мебели и т. д.
Здесь также можно выделить «зону карантина», куда потом все предметы с красными ярлыками будут стекаться для рассмотрения: нужны они или нет и как их перераспределить. Здесь тот же принцип — делим предметы на нужные и ненужные. Все, в чем сомневаемся, все, что нам не нужно, — на все это крепим красный ярлык и свозим в зону карантина. Учитываем, регистрируем и принимаем решение, куда это все девать.
Форма красных ярлыков может быть совершенно разной (см. рисунок выше). Могут быть очень простые ярлычки, в виде бирок, например, а могут быть достаточно сложные и объёмные. Если вы пользуетесь системой красных ярлыков, рекомендуем вам делать и ярлыки, и порядок работы как можно проще.
Все красные ярлыки объединяет несколько общих категорий данных. Это название предмета либо производственный номер предмета, категория предмета (все предметы можно разделить по категориям), количество предметов. Кроме этого, указываются причины, почему к предмету прикреплен красный ярлык. Например, он не используется для текущих операций, содержит дефект или излишнее количество дубликатов. Пишется подразделение, в чьем ведении находится данный предмет, иногда пишут стоимость предмета. Обычно всегда пишут дату, когда предмет помечен красным ярлыком. В некоторых местах отмечают способ удаления — утилизировать, передать на склад и т. д.
Это суть метода. Проводить вам ее или нет — это ваш выбор, вы решаете сами. При проведении сортировки — это то, что вы сортируете предметы на нужные и ненужные, выделяете карантинную зону, куда вы могли бы временно переместить ненужные предметы и предметы, в которых вы сомневаетесь. Постарайтесь максимально исключить возврат ненужных предметов на рабочее место. Если красный ярлык сигнализирует о том, что предмет на рабочем месте не нужен, то, если вы его не используете, риск возврата предмета на рабочее место увеличивается. Поэтому обратите на это внимание.
Второй шаг — Соблюдение порядка
Рассмотрим второй шаг 5S — соблюдение порядка или упорядочивание.
Теперь, когда вы избавились от лишних предметов, следует организовать хранение необходимых вещей так, чтобы можно было их быстро найти и использовать.
Суть этого шага сводится к такой организации хранения необходимых предметов и вещей, которая позволяла бы быстро и просто их найти и использовать.
Речь идёт о рациональном размещении предметов в соответствии с требованиями безопасности, качества и производительности труда, которое бы минимизировало время и усилия по нахождению этих предметов.
Часто мы можем видеть такие примеры в различных источниках (см. рисунок выше). Если такое размещение позволяет рабочему быстро увидеть и использовать предмет и потом быстро положить на место, то это вполне хорошее решение.
Однако, существует в настоящее время очень много примеров, созданных не для того, чтобы рационально использовать предметы, а для того, чтобы показать, что существует некое подобие производства. Я сам часто встречал такое положение инструмента, когда он был просто прибит к стене. Это уже не наш подход и эту ситуацию мы затрагивать не будем.
Если напротив рабочего места размещен такой стенд, и рабочий каждый день использует в своей работе отвертки, ножовку, дрель, долото и т.д., то такое размещение инструментов оправдано. Оно обеспечивает быстроту и простоту нахождения и использования инструмента.
Чтобы реализовать этот шаг, нужно сделать четыре основных действия:
1. Определить места хранения предметов. Мы уже знаем, что конкретно необходимо держать на рабочем месте.
2. Определить, где это должно находиться с учетом того, чтобы можно было быстро найти и использовать. Чтобы было безопасно, не тратилось дополнительное время и усилия по нахождению нужных предметов, чтобы это не влияло на качество и так далее.
3. Определить способ хранения предмета (кладем, подвешиваем, ставим и т.д.). Способ хранения инструмента должен обеспечивать безопасность. Например, мы никогда не ставим ножи острыми концами вверх. Способ хранения инструментов должен обеспечивать быстроту, оперативность его забора, а также качество выполнения работ. Если мы, например, храним металлический инструмент в месте, где повышенная влажность, то это впоследствии может отразиться на качестве работы.
4. Обеспечить соблюдение правил размещения. Как правило, это визуализация выделенных зон. Не уделяйте больше места, чем это необходимо, исключайте возможность хранения лишних предметов. Сделайте место и способ хранения основных предметов таким, чтобы туда было невозможно положить тот предмет, который не используется.
Невозможно ничего другого разместить потому, что там находится именно минимальный набор самого необходимого. Способ размещения в ящиках, на полочках, различные способы оконтуривания препятствуют размещению каких-либо лишних предметов в местах хранения основного инструмента.
Основная цель второго шага — это повышение производительности за счет уменьшения потерь времени на поиск и получение необходимых предметов.
Основная задача — это определение необходимых предметов в зоне рабочего места и нахождение лучшего места для их размещения.
Эффективность от внедрения второго шага выражается в уменьшении потерь времени на поиск необходимых инструментов, предметов и документов. В уменьшении запасов материальных ценностей за счет исключения лишних предметов, в улучшении качества за счет исключения возможности ошибочного использования инструментов или предметов, за счет уменьшения травмоопасных ситуаций, улучшения морального настроя персонала, комфортной организации рабочих мест.
При организации хранения необходимых для работы предметов на рабочем месте необходимо ориентироваться на удобство и безопасность для рабочего. Нужно делать так, чтобы было легко взять и вернуть на место. Отсутствие любого предмета должно быть видно. Предметы не должны мешать работе и перемещениям. Должна быть обеспечена сохранность предметов и поддержание установленного порядка каждый день.
Например, в приведённых выше простых примерах осуществлена возможность быстро взять предмет и положить на место, даже при отсутствии предмета легко понять, что и где должно храниться.
Основные способы организации рабочих предметов — это разметка, оконтуривание, подписи, перечни с указанием количества, даты и прочей информации, держатели инструмента из подручных средств.
Не стремитесь изготавливать какие-то специальные тумбочки, стеллажи для хранения вещей. Все можно сделать из подручных средств. Например, на одном из рисунков выше хранение инструмента организовано с использованием простого туристического коврика. Из любых подручных материалов можно организовать упорядоченное хранение инструментов. Выше пример визуализации расположения рулона бумаги. Место обозначено, оконтурено. Если рулон поставят куда-то в другое место — то это сразу же будет видно.
Для офиса может быть применено различное упорядочивание папок, визуализация, цветовая маркировка, перечни, подписи, разделение по категориям.
Итак, на втором шаге 5S проводится упорядочивание оставшихся предметов, оставляется оптимальное их количество и каждому предмету определяется свое постоянное место расположения исходя из критериев максимальной эффективности выполнения работ. Максимальная эффективность подразумевает возможность быстрее и удобнее взять в работу, не искать, безопасно работать, не оказывая негативного влияния на качество. Место должно быть обозначено. Соблюдение правил размещения можно обеспечить, визуализировав предметы, их места нахождения. Следует максимально исключить возможность попадания ненужных вещей в место хранения основных.
Третий шаг — Содержание в чистоте
В данном разделе речь пойдет про третий шаг организации рабочих мест 5S, он называется «содержание в чистоте» (SEISO). Его еще часто называют «уборка».
Суть этого шага отражена в его названии — наведение и поддержание чистоты и опрятности на рабочем месте. Это создание благоприятных условий содержания оборудования, рабочих мест, которое способствует, в свою очередь, повышению производительности труда, улучшению качества продукции и так далее.
Если рассматривать работу оборудования, то чистка и уборка рабочих мест — это еще и проверка, диагностика оборудования, выявление неисправностей, которые могут перерасти в поломку. Это также изучение оборудования и того рабочего места, на котором работает работник. Внедрение третьего шага уменьшает потери, простои оборудования, улучшается надежность его работы, вовремя выявляются утечки, качество продукции повышается, исключается возможность травм, улучшается моральный настрой персонала за счет комфорта рабочих мест.
Главное на этом этапе — выявить проблемы, которые скрываются за загрязнениями, обеспечить поддержание чистоты и порядка. Для этого проводят общую уборку рабочего пространства: выкидывают мусор, вычищают грязь, красят оборудование.
Рассматриваются причины загрязнений: откуда что сыплется или капает и т. д. Когда мы лично убираем мусор, нам уже не хочется видеть его снова. Поэтому и рассматриваются причины загрязнений, которые должны быть незамедлительно ликвидированы. Там, где невозможно устранить причину загрязнения, проводят их локализацию: улучшают сбор загрязнений, их отвод и так далее.
На этом этапе нужно определить правила поддержания чистоты. После того, как мы в первый раз прошли все три шага, мы уже понимаем, с какой периодичностью необходимо за оборудованием ухаживать, чтобы оно поддерживалось в рабочем состоянии.
Суть шага — в чистке инструментов, рабочего места и поверхностей, того, что находится на рабочем месте и вокруг него.
Не стоит полагаться на рабочего, чтобы он выполнил самостоятельно всю чистку и уборку. 5S — это работа командная и она должна выполняться группой с участием человека, который непосредственно работает на данном рабочем месте. Помните, что генеральная уборка не должна отразиться на выполнении плана.
Окраска оборудования и рабочих поверхностей в светлые цвета облегчает впоследствии обнаружение грязи и подтёков (например, масла). Многие бережливые заводы стараются при покраске оборудования использовать светлые тона для того, чтобы любое загрязнение сразу бросалось в глаза. К тому же визуально становится светлее, благодаря этому можно легче обнаружить источники загрязнения, трещины, незакрученные гайки и болты, это относится не только к оборудованию, но и к приспособлениям, столам, в целом к рабочим местам.
При рассмотрении причин загрязнений, нам следует понять, откуда течет, сыплется, откуда капает. Столкнувшись с большим загрязнением, нужно понять, как оно здесь оказалась? На этом шаге выявляются критические неисправности оборудования. Наиболее распространенные из них — это течи масла, охлаждающих жидкостей, просипи материала и т. д.
Здесь выявляются внешние и общие источники загрязнения (те, которые находятся вне рабочего места). На это нужно обращать внимание и стараться при организации рабочих мест немного выходить за рамки конкретного рабочего места.
Часто выявляется отсутствие элементарного обеспечения, например, когда мы рассматриваем источники загрязнения оборудования, мы можем увидеть, что где-то нет мусорных корзин, умывальника, не хватает ветоши, салфеток (необходимо для того, чтобы выполнять постоянно уборку). Возможно, источники загрязнения не такие серьезные, чтобы обращать на них внимание. Но, возможно, грязь копится из-за того, что ее нечем или некуда убрать. Рабочий бы и рад вытереть, но ему нечем, а своей рубашкой он этого делать не хочет. Это тоже достаточно распространенное явление.
На стадии устранения причин загрязнений происходит наладка и ремонт оборудования, где это можно сделать. Важно, что если вы не можете что-то устранить сразу же, то источник загрязнения всегда можно локализовать.
Самые распространенные варианты локализации, например, поддоны для сбора жидкостей, укрытия от протечек и просипи, дополнительные вентиляционные короба, которые помогают собирать пыль. Это может быть все, что угодно.
На рисунке, например, представлен штамповочный станок, отходы которого отлетали в радиусе 2 м от станка. Впоследствии была прикреплена деревяшка, но отходы все равно отлетали примерно на метр. Потом к станку прикрепили половину файлика и сбор загрязнений был практически полностью локализован. Вся стружка собирается на маленький поддон. Это один из примеров.
Ниже на рисунке приведён пример не очень красивого, но простого решения. От течи масла избавиться не удалось, но загрязнения были локализованы простым способом: поддон, отверстие и ведро. Вы всё видите сами.
Далее следует определение правил поддержание чистоты. Необходимо определить объекты для регулярной уборки. Это может быть рабочая зона оборудования, верстак, инструментальная тумбочка: то, что постоянно необходимо убирать, где скапливается больше всего грязи. Для того, чтобы рабочее место содержать в нормальном виде, необходимо определить места наибольшего скопления хлама. Потом создается обеспечение средствами уборки, определяется место для сбора отходов и т. д.
Нужно обеспечить работнику условия для того, чтобы он мог самостоятельно проводить уборку. Если мусорной корзины, тряпки и т. д. нет, то мусор будет скапливаться. Также здесь рекомендуется разделить участок на зоны ответственности, назначить ответственных за поддержание чистоты рабочей зоны. Это важно, ведь на рабочем месте часто бывает более одного «хозяина», т.е. работающих на территории сотрудников. В таком случае следует разделить либо ответственность, либо рабочую зону.
Места общего пользования можно разделить поровну. Нужно создать элементарные правила, которые должны быть сформулированы не просто руководителем команды, а вместе с работниками, непосредственно работающими на данном рабочем месте.
В четвертом шаге определяют время уборки, ее периодичность, разрабатываются графики уборки на рабочих местах. Для того, чтобы чистоту поддерживать, нужны реальные ресурсы, например, ведро, перчатки, швабра, и ресурсы временные. Например, 5—10 минут в конце смены для того, чтобы прибраться на рабочем месте перед уходом и передать его по смене. Здесь же устанавливаются критерии чистоты, которые обычно документируются. Например, отсутствие разводов на стекле, не пронумерованных папок и т. д. Рождаются некие формализованные правила.
После устранения источников загрязнения в завершение уборки очень важным элементом является информирование персонала и обеспечение контроля. Именно для этого и устанавливаются правила. Не для того, чтобы были созданы новые бумаги по обеспечению чистоты на рабочем месте, а для того, чтобы обеспечить контроль и выработать привычку.
Мы рассмотрели несколько примеров стандартов, несмотря на то, что стандартизация — это четвертый шаг 5S. Если вы заметили, во всех разделах мы немного забегаем вперед, чтобы уже до начала следующего шага вы начинали готовить почву для реализации следующего шага.
Пока вы прибираетесь, приводите в нормальное состояние рабочие места, устраняете источники загрязнения и понимаете, как часто нужно убираться с учетом оставшихся источников загрязнения и определяются критерии чистоты. Наведение чистоты и порядка на рабочем месте в большей степени влияет на качество продукции, в меньшей степени на эстетику рабочих мест, об этом нужно помнить. Очень много потерь образуются из-за нерациональной организации рабочих мест.
На третьем шаге 5S необходимо определить источники загрязнения, устранить все течи и просыпания, устранить загрязнение оборудования, очистить инструмент, оснастку. Кроме того, определить базу для стандарта ежедневной уборки, назначить ответственных, разграничить зоны, определить параметры и критерии чистого рабочего места и периодичность уборки рабочих мест (кто это должен сделать, чем, как часто).
Четвертый шаг — стандартизация
В данном разделе речь пойдет про четвертый шаг 5S — стандартизацию (SEIKETSU).
Его цель — обеспечение выполнения требований к рабочему месту, которые были сформулированы и выполнены в первых трех шагах.
Это необходимое условие для выполнения первых трех шагов.
Основная задача этого шага — стандартизировать условия и критерии состояния рабочего места.
Стандартизировать можно двумя основными способами. Во-первых, с помощью средств визуального контроля, во-вторых, с помощью документирования: создания, разработки либо изменения какого-либо документа.
Что мы получаем от шага стандартизации? Исключение возможности возвращения исходного состояния. Стандарт препятствует возврату в исходное состояние. Когда мы создаем инструкции о поддержании рабочего места в порядке, мы также обеспечиваем возможность оценки состояния рабочего места, обеспечиваем возможность контроля за его нормальным состоянием. Кроме того, стандарт обеспечивает условия для дальнейшего совершенствования рабочего места. Уменьшение потерь происходит за счет создания правил организации рабочего пространства, которые включают фактические действия работников.
Поддержание процесса организации рабочего места — это часть ежедневной работы каждого. Это помощь в ежедневной работе руководителя по контролю за состоянием рабочих мест (с помощью стандарта руководитель может понимать разницу между фактическим состоянием рабочих мест и тем, что прописано в стандарте). Это напоминание для рабочего (как должно быть, как поддерживать рабочие места в нормальном состоянии).
Стандарт рабочего места должен содержать пункты о разделении зоны ответственности, самих ответственных, что именно должно убираться, как и так далее.
Существует картинка с символичным колесом улучшений, которая показывает суть работы стандарта. Чтобы крутилось такое колесо, надо проделать определенную работу, и кроме того, приложить определенные усилия к тому, чтобы система не вернулась в первоначальное состояние. Это обусловлено законом сохранения энергии, то есть если улучшение не стандартизировать, оно вернется в первоначальное состояние. Чтобы это предотвратить и существует символический клин под названием «стандарт». Он мешает улучшению регрессировать, откатиться назад. Даже существует такой устоявшийся термин, как откат — возврат улучшения в первоначальное состояние.
Применительно к организации рабочих мест, можно говорить о том, что, если вы провели кампанию по сортировке, упорядочиванию, наведению чистоты и просто ушли, через некоторое время вы обнаружите, что улучшения просто исчезли и все вернулось в первоначальное состояние. Появились такие же источники загрязнения, мусор опять лежит повсюду, валяются лишние предметы и так далее.
Это нормальное явление, обычно так и происходит если результат не стандартизировать и не доводить работу до четвертого и пятого шага: до выработки привычки. Применительно к другим инструментам или методам, также после любого улучшения должен быть период плотного контроля, выработки привычки. Постепенно, после того, как привычка начинает вырабатываться, контроль можно будет немножко ослабить таким образом, чтобы колесо улучшений не откатывалось.
По определению, стандарт — это то, как должно быть. Это может быть состояние рабочего места, порядок уборки, неважно. Стандарт всегда отражает с точки зрения бережливого производства наилучший вариант развития событий. Если речь идёт о стандарте выполнения работы — то это лучшая последовательность действий с минимальным количеством потерь, наиболее безопасная, эргономичная, обеспечивающая максимальную производительность. Если мы говорим об организации рабочего пространства, стандарт содержит наилучший способ организации такого пространства, обеспечивающий максимальную эффективность работы в этом пространстве, минимальные потери времени на поиск предметов, сортировку, перекладывание и т. д.
Когда мы говорим про стандартизацию, мы понимаем под этим термином не только разработку или изменение какого-либо документа, но и создание условий в целом для того, чтобы улучшение не вернулось в первоначальное состояние.
Такими условиями могут быть какие-то физические изменения рабочих мест. Например, вы перенесли принтер, чайник, оборудование, оснастку, телефон на другое место, что позволило экономить какие-то секунды, метры и т. д. Вы можете стандартизировать этот результат, например, разработав какой-то документ, в котором прописано, что данная вещь стоит здесь, или собирается здесь, а это находится здесь, и так далее. С другой стороны, вы можете обеспечить условия для того, чтобы улучшения прижились и не вернулись в обратное состояние. Например, вы можете демонтировать розетки, чтобы прибор не поставили обратно, заглушить какие-то краны, вы можете, перенеся рабочее место, обеспечить там питание, а в старом месте его заглушить и т. д.
Такие действия гораздо эффективнее, чем стандарты в виде документов, они не требуют контроля. Это элемент защиты от ошибок, который тоже относится к стандартизации, это тоже создание условий для того, чтобы улучшение прижилось и не вернулось в первоначальное состояние.
Стандартизация — важный шаг, позволяющий не только закрепить достигнутые результаты, но и подготовить плацдарм для дальнейших улучшений.
Сущность шага заключается в закреплении достигнутых результатов. Это осуществляется с помощью понятных правил и процедур, обязательных к исполнению и обеспечивающих поддержание ранее достигнутого состояния.
Обычно делаются следующие вещи:
— разработка либо изменение стандартов, инструкций и правил, какой-то документации;
— обеспечение возможности визуального контроля;
— обучение персонала, которое проходит после реализации первых 2 направлений, когда появляется уже какой-то документ, утвержденный стандарт, и после того, как появляется возможность визуального контроля.
Что обычно стандартизируют?
Стандартизировать можно все, что угодно. Применительно к рабочим местам можно выделить несколько типичных направлений.
Расположение передвижного инвентаря, стеллажей, тумбочек, столов и т. д. Такие вещи обычно стандартизируют с помощью оконтуривания, разметки, визуализации, планировок, они позволяют зафиксировать то состояние, которое должно быть.
Часто визуализируют наличие и расположение инструмента, где оно должно размещаться. Например, на рисунке ниже визуализированы канцтовары — подписи, сколько чего должно быть.
Стандартизируют правила и критерии поддержания чистоты и выполнения уборок, то, что было сделано на третьем шаге. Например, на рисунке выше представлен стандарт уборки на рабочем месте, визуальные подсказки, механизм действий, краткие пояснения. Лучший стандарт — визуальный. Если у вас есть возможность, старайтесь не писать много текста, вешать распоряжения, лучше любой стандарт сделать с помощью схем, фотографий, графической информации. Она усваивается гораздо быстрее и откладывается в голове намного глубже, т.е. поддерживать информированность людей с помощью визуальных стандартов намного проще, чем с помощью текста.
5S — это… Что такое 5S?
5S — система организации и рационализации рабочего места. Была разработана в послевоенной Японии.
5S — это пять японских слов:
- Сэири (整理) «сортировка» — чёткое разделение вещей на нужные и ненужные и избавление от последних.
- Сэитон (整頓) «соблюдение порядка» (аккуратность) — организация хранения необходимых вещей, которая позволяет быстро и просто их найти и использовать.
- Сэисо (清掃) «содержание в чистоте» (уборка) — соблюдение рабочего места в чистоте и опрятности.
- Сэикэцу (清潔) «стандартизация» (поддержание порядка) — необходимое условие для выполнения первых трёх правил.
- Сицукэ (躾) «совершенствование» (формирование привычки) — воспитание привычки точного выполнения установленных правил, процедур и технологических операций.
Цели 5S
- Снижение числа несчастных случаев
- Повышение уровня качества продукции, снижение количества дефектов
- Создание комфортного психологического климата, стимулирование желания работать
- Повышение производительности труда (что в свою очередь ведёт к повышению прибыли предприятия и соответственно повышению уровня дохода рабочих).
Принципы 5S
Сортировка
Все материалы, оборудование и инструмент сортируют на:
- нужные всегда — материалы, которые используются в работе в данный момент;
- нужные иногда — материалы, которые могут использоваться в работе, но в данный момент не востребованы;
- ненужные — брак, неиспользуемые инструменты, тара, посторонние предметы.
В процессе сортировки ненужные предметы помечают «красной меткой» и затем удаляют из рабочей зоны.
Соблюдение порядка
Расположение предметов отвечает требованиям:
Четыре правила расположения вещей:
- на видном месте;
- легко взять;
- легко использовать;
- легко вернуть на место.
Содержание в чистоте
Рабочая зона должна поддерживаться в идеальной чистоте.
Порядок действий:
- Разбить линию на зоны, создать схемы и карты с обозначением рабочих мест, мест расположения оборудования и т. п.
- Определить специальную группу, за которыми будет закреплена зона для уборки.
- Определить время проведения уборки:
- утренняя: 5-10 мин. до начала рабочего дня
- обеденная: 5-10 мин. после обеда
- по окончании работы: после прекращения работы, во время простоев
Стандартизация
Этот принцип требует формального, письменного закрепления правил содержания рабочего места, технологии работы и других процедур.
Необходимо создать рабочие инструкции, которые включат в себя описание пошаговых действий по поддержанию порядка. А также вести разработки новых методов контроля и вознаграждения отличившихся сотрудников.
Совершенствование
Выработка привычки ухода за рабочим местом в соответствии с уже существующими процедурами, а также неуклонное совершенствование самой системы.
Важные моменты:
- Наблюдение за работой оборудования, за рабочим местом, чтобы облегчить их обслуживание.
- Использование фотографий ДО/ПОСЛЕ для сравнения того, что было, и какой конечный результат.
- Организация аудитов, чтобы оценить эффективность внедрения программы 5S.
Философия 5S
Некоторых вводит в заблуждение формулировка данной концепции.
5S — это не просто «стандартизация уборки». 5S — это философия малозатратного, успешного, бережливого производства.
Данная философия/концепция производства подразумевает, что каждый сотрудник предприятия от уборщицы до директора выполняют эти 5 простых правил. Основной плюс — эти действия не требуют применения новых управленческих технологий и теорий.
Внедрение
Одна из популярных методик внедрения системы предлагает разбить процесс внедрения на 5 этапов[1]:
- Ознакомление с принципами и принятие системы
- Наведение порядка и делегирование ответственности
- Регулярность действий и периодический контроль
- Закрепление процедур и усиление требований
- Постоянное совершенствование
На очередном этапе фиксируется достижение определенных показателей по каждому из пяти слагаемых 5S, что позволяет придать внедрению планомерную форму и сократить сопротивление персонала изменениям. При таком подходе обеспечивается более полное вовлечение всех работников в процесс.
Примечания
Ссылки
Рекомендованные книги
Принципы и инструменты бережливого производства системы 5S
Система 5S – один из ключевых инструментов бережливого производства, направленный на повышение безопасности, эффективности и производительности труда на рабочем месте (рабочем пространстве). Благодаря своей простоте и эффективности часто является начальным этапом совершенствования производственной системы. При этом реализация данной методики формирует новую культуру производства, позволяющую качественно изменить организацию.
Название метода происходит от 5 шагов, каждый из которых начинается на “С”. Так как систему придумали в Японии, оригинальные названия читаются примерно так: Seiri, Seiton, Seiso, Seiketsu, Shitsuke. Позже 5 этапов внедрения были переведены на английский: Sort, Straighten, Sweep, Standardize, Self-discipline, – и русский. Один из вариантов русского перевода: Сортировка, Самоорганизация, Сияние, Стандартизация, Совершенствование. Из-за наличия русского перевода этапов название системы можно встретить как в латыни (5S), так и русскоязычном варианте (5С).
Примечателен тот факт, что схожая система – CANDO (Clearing, Arrangement, Neatness, Discipline, Organization), – появившаяся в США намного раньше, чем 5S, в наши дни менее известна и распространена. По некоторым источникам, CANDO – один из тех принципов бережливого производства, которые основатель производственной системы Toyota позаимствовал во время визита на завод Ford.
Первый шаг системы 5S – Сортировка
На данном этапе все мероприятия сводятся к определению необходимых для работы инструментов и удалению всех ненужных, неисправных или неиспользуемых предметов. Для чего это делается? Для повышения безопасности на рабочем месте, стандартизации выполняемой работы – соответственно, повышения продуктивности и качества.
Практики бережливого производства называют этот шаг самым сложным, так как признавать ненужность предметов, которые долгое время находились под рукой, для большинства людей не так просто. В психологическом плане это требует отказа от привычного порядка, сформировавшегося за годы работы, и принятия нового, неизвестного, часто насаждаемого извне.
Для того, чтобы преодолеть сопротивление на этом этапе, чаще всего прибегают к трем приемам:
- Проводят обучение принципам бережливого производства и системы 5S.
- Вовлекают сотрудников в процесс реализации системы 5S на их непосредственных рабочих местах.
- Создают зону “красных меток” (Red Tag Area) – карантин для предметов, которые не используются на рабочем месте ежедневно, однако по тем или иным причинам не могут быть удалены немедленно.
Второй шаг системы 5S – Самоорганизация или систематизация
Как говорят практики бережливого производства: “всему свое место, и все на своих местах”. Данный этап нацелен на максимально рациональное размещение необходимых для работы предметов в рабочем пространстве. Чем чаще используется предмет, тем ближе и доступнее он должен быть расположен. Чем реже – тем больше шансов найти его за пределами рабочего места, например, в шкафу или на общем стенде.
Зачем это делается? Опять же, безопасность, продуктивность и качество. Удобно расположенный предмет обеспечит эргономику рабочего места и целевое применение. Те же инструменты, которые используются реже, следует разместить в поле общего доступа, что существенно сократит их необходимое количество.
Основные приемы данного этапа системы 5С – различные варианты визуализации: маркировка, зонирование, оконтуривание, метод “теней” и т.д.
Третий шаг системы 5S – Сияние или содержание в чистоте
Данный этап направлен на создание условий для поддержания чистоты рабочего пространства. Разумеется, это подразумевает уборку и чистку. Но на этом третий шаг внедрения системы 5С не завершается. Необходимо установить источники загрязнения – понять причины и разработать план мероприятий по их устранению.
Также на данном этапе разрабатываются графики и стандарты уборки (кто, как часто и чем проводит уборку?), а также обеспечивается необходимых для этих целей инвентарь.
Четвертый шаг системы 5S – Стандартизация
Стандартизация предполагает меры по закреплению и удержанию достигнутых результатов. Для этих целей разрабатываются организационные стандарты, которые в лаконичной и визуализированной форме закрепляют правила относительно обустройства, визуализации, уборки, зонирования и других параметров рабочих мест.
Кроме того, настоящий этап предусматривает создание системы контрольных механизмов, чаще всего аудитов 5С. Для чего это делается? Чтобы предотвратить постепенное “скатывание” системы к первоначальному состоянию.
Пятый шаг системы 5S – Совершенствование
Как проще всего обеспечить удержание полученных результатов? Только непрерывно совершенствуя рабочее пространство усилиями всех сотрудников: каждый сотрудник, каждый день, всюду!
На данном этапе применяют следующее:
- Обеспечивают информирование персонала о состоянии процесса развертывания системы 5S, результатах аудитов, выявленных проблемах и т.д.
- Обеспечивают интеграцию системы 5S и системы подачи предложений по улучшениям.
- Обеспечивают интеграцию системы аудитов 5S и премирования сотрудников.
Что такое 5S? Объясняется система 5S, включая советы по запуску программы 5S.
5S — это система для организации пространства, позволяющая выполнять работу эффективно, результативно и безопасно. Эта система нацелена на то, чтобы разместить все на своих местах и поддерживать чистоту на рабочем месте, что позволяет людям выполнять свою работу, не теряя времени и не рискуя получить травмы.
Перевод 5S
Термин 5S происходит от пяти японских слов:
- Сейри
- Сейтон
- Seiso
- Сэйкэцу
- Сицукэ
В английском языке эти слова часто переводят на:
- Сортировать
- На заказ
- Блеск
- Стандартизация
- Сустейн
Каждый S представляет собой одну часть пятиэтапного процесса, который может улучшить общую функцию бизнеса.
Истоки 5S — 5S и бережливое производство
5S началось как часть производственной системы Toyota (TPS), метода производства, начатого руководителями Toyota Motor Company в начале и середине 20 века. Эта система, которую на Западе часто называют бережливым производством, направлена на повышение ценности продуктов или услуг для клиентов. Это часто достигается путем поиска и устранения отходов производственных процессов.
Бережливое производство предполагает использование многих инструментов, таких как 5S, кайдзен, канбан, дзидока, хейдзунка и пока-иго.5S считается основополагающей частью производственной системы Toyota, потому что до тех пор, пока рабочее место не будет чистым и организованным, добиться стабильно хороших результатов будет сложно. Грязное, загроможденное пространство может привести к ошибкам, замедлению производства и даже несчастным случаям, которые прерывают работу и негативно влияют на компанию.
Имея систематически организованное производство, компания увеличивает вероятность того, что производство будет происходить именно так, как должно.
Преимущества 5S
Со временем методология 5S дает множество преимуществ, в том числе:
- Сниженные затраты
- Более высокое качество
- Повышенная производительность
- Повышение удовлетворенности сотрудников
- Более безопасная рабочая среда
Что такое 5 S?
Концепция 5S может показаться немного абстрактной на данном этапе, но на самом деле это очень практичный практический инструмент, частью которого может стать каждый на рабочем месте.
5S включает в себя оценку всего присутствующего в пространстве, удаление ненужного, логическую организацию вещей, выполнение служебных задач и поддержание этого цикла. Организуйте, уберите, повторите.
Рассмотрим подробнее каждую из частей 5S.
Сортировка
Первый шаг 5S, Сортировка, включает в себя просмотр всех инструментов, мебели, материалов, оборудования и т. Д. В рабочей зоне, чтобы определить, что должно быть в наличии, а что можно удалить. Вот некоторые вопросы, которые нужно задать на этом этапе:
- Какова цель этого предмета?
- Когда последний раз использовался этот предмет?
- Как часто это используется?
- Кто им пользуется?
- Он действительно должен быть здесь?
Эти вопросы помогают определить стоимость каждого предмета.Рабочее пространство может быть лучше без ненужных элементов или элементов, которые используются нечасто. Эти вещи могут мешать или занимать место.
Помните, что лучшие люди для оценки предметов в пространстве — это люди, которые в нем работают. Именно они могут ответить на поставленные выше вопросы.
Когда группа определила, что некоторые элементы не нужны, рассмотрите следующие варианты:
- Передать товары в другой отдел
- Переработать / выбросить / продать предметы
- Сдать вещи на хранение
В случаях, когда значение элемента не определено — например, инструмент не использовался в последнее время, но кто-то думает, что он может понадобиться в будущем — используйте метод red tag .Красные бирки обычно представляют собой картонные бирки или наклейки, которые можно прикрепить к рассматриваемым предметам. Пользователи заполняют информацию о предмете, такую как:
- Расположение
- Описание
- Имя лица, применившего тег
- Дата подачи заявки
Затем этот предмет помещается в «зону красных ярлыков» вместе с другими сомнительными предметами. Если по прошествии определенного времени (возможно, месяц или два) элемент не использовался, пора удалить его из рабочей области.Не стоит цепляться за вещи, которые никогда не используются, поскольку они просто занимают место.
Совет: Установите напоминание — на вашем телефоне или компьютере или отправьте где-нибудь в рабочем пространстве — чтобы отметиться снова с помощью красной области метки, чтобы о нем не забыли.
Заказ
Когда лишний беспорядок исчезнет, станет легче увидеть, что к чему. Теперь рабочие группы могут придумывать свои собственные стратегии сортировки оставшихся элементов. На заметку:
- Какие люди (или рабочие станции) какими предметами пользуются?
- Когда используются предметы?
- Какие предметы используются чаще всего?
- Следует сгруппировать элементы по типу?
- Где было бы логичнее всего разместить предметы?
- Могут ли некоторые рабочие места быть более эргономичными для рабочих, чем другие?
- Могут ли некоторые размещения сократить ненужное движение?
- Нужно ли больше контейнеров для хранения вещей?
На этом этапе каждый должен определить, какие аранжировки наиболее логичны.Для этого потребуется продумать задачи, частоту выполнения этих задач, пути, по которым люди проходят через пространство, и т. Д.
Компании могут захотеть остановиться и подумать о взаимосвязи между организацией и более крупными усилиями по бережливому производству. Какое устройство вызовет наименьшее количество отходов?
При бережливом производстве отходы могут иметь следующий вид:
- Дефекты
- Время ожидания
- Дополнительное движение
- Избыточные запасы
- Перепроизводство
- Дополнительная обработка
- Ненужная транспортировка
- Неиспользованные таланты
Совет: Для целей 5S, в частности, рассмотрите, как планировка и организация области могут увеличить / уменьшить время ожидания, движение и ненужную транспортировку.
Блеск
Все думают, что знают, что такое ведение домашнего хозяйства, но это одна из самых простых вещей, которые можно упустить из виду, особенно когда на работе много работы. Этап Shine в 5S направлен на уборку рабочей зоны, что означает подметание, мытье полов, вытирание пыли, протирание поверхностей, размещение инструментов и материалов и т. Д.
Помимо основной очистки, Shine также включает регулярное техническое обслуживание оборудования и механизмов. Заблаговременное планирование технического обслуживания означает, что предприятия могут выявить проблемы и предотвратить поломки.Это означает меньшую потерю времени и отсутствие потери прибыли, связанной с остановками в работе.
Освещение рабочего места может показаться неприятным, но это важно. И это не следует оставлять на усмотрение обслуживающего персонала. В 5S каждый берет на себя ответственность за уборку своего рабочего места, в идеале — ежедневно. Это побуждает людей брать на себя ответственность за пространство, что в конечном итоге означает, что люди будут больше инвестировать в свою работу и в компанию.
Совет: Способ очистки может показаться очевидным, но убедитесь, что люди знают, как правильно осветить свое пространство.Покажите сотрудникам, особенно новым сотрудникам, какие чистящие средства использовать, где хранятся чистящие средства и как чистить оборудование, особенно если это оборудование можно легко повредить.
Стандартизация
После завершения первых трех шагов 5S все должно выглядеть неплохо. Все лишнее убрано, все организовано, помещения убраны, оборудование в хорошем рабочем состоянии.
Проблема в том, что когда 5S является новым для компании, его легко очистить и организовать… а затем постепенно позволить вещам вернуться на круги своя.Стандартизация отличает 5S от типичного проекта генеральной уборки. Стандартизация систематизирует все, что только что произошло, и превращает разовые усилия в привычки. Стандартизация назначает регулярные задачи, создает расписания и публикует инструкции, чтобы эти действия превратились в рутину. Он устанавливает стандартные операционные процедуры для 5S, чтобы упорядоченность не отводилась на второй план.
В зависимости от рабочего пространства может быть полезен ежедневный контрольный список 5S или диаграмма. Еще одним полезным инструментом является опубликованное расписание с указанием того, как часто должны выполняться определенные задачи по очистке и кто за них отвечает.
Изначально людям наверняка понадобятся напоминания о 5S. Может потребоваться ежедневно выделять небольшое количество времени для задач 5S. Но со временем задачи станут рутинными, а организация и уборка 5S станут частью регулярной работы.
Совет: Визуальные подсказки, такие как знаки, этикетки, плакаты, лента для разметки пола и органайзеры для инструментов, также играют важную роль в 5S. Они могут указать направление и держать предметы на месте, во многих случаях без слов.
Сустейн
После внедрения стандартных процедур для 5S предприятия должны выполнять текущую работу по поддержанию этих процедур и их обновлению по мере необходимости.Устойчивость относится к процессу обеспечения бесперебойной работы 5S, но также и к вовлечению всех сотрудников организации. Менеджеры должны участвовать, как и сотрудники на производстве, на складе или в офисе. Sustain делает 5S долгосрочной программой, а не просто мероприятием или краткосрочным проектом. В идеале 5S становится частью культуры организации. И когда 5S будет поддерживаться в течение долгого времени, именно тогда предприятия начнут замечать постоянные положительные результаты.
Совет № 1: Чтобы поддерживать практику 5S, убедитесь, что все новые сотрудники (или сотрудники, которые меняют отдел) прошли обучение процедурам 5S в их районе.
Совет № 2: Сохраняйте интерес. Посмотрите, что другие компании делают с 5S. Новые идеи для организации могут улучшить ситуацию и сохранить вовлеченность сотрудников.
Безопасность — Шестой S
Некоторым компаниям нравится включать шестую букву S в свою программу 5S: безопасность. Когда включена безопасность, систему часто называют 6S. Этап безопасности включает в себя сосредоточение внимания на том, что можно сделать для устранения рисков в рабочих процессах, организовав вещи определенным образом.
Это может включать настройку рабочих станций, чтобы они были более эргономичными, маркировку перекрестков — например, места пересечения погрузчиков и пешеходов — знаками и маркировку шкафа для хранения химикатов, чтобы люди знали о потенциальных опасностях.Если планировка рабочего места или выполняемые людьми задачи опасны, эти опасности следует уменьшить в максимально возможной степени. Вот на что ориентирована шестая S.
Некоторые люди считают безопасность результатом правильного выполнения пяти других S и в результате говорят, что шестая S не нужна. Они думают, что если рабочее пространство правильно организовано и убрано, а также используются полезные визуальные сигналы безопасности, отдельный шаг безопасности не нужен.
Ни один из подходов к безопасности не является правильным или неправильным.Но как бы бизнес ни хотел подходить к безопасности, следует осознавать, что внимание к безопасности важно.
Совет: Если неудачи и несчастные случаи все же случаются, остановитесь и подумайте, могло ли улучшение 5S предотвратить это. Могли ли изменить ситуацию меньший беспорядок, более чистые пешеходные дорожки или лучшие знаки и надписи?
Начало работы с 5S
Несмотря на то, что 5S — довольно простая концепция, запуск новой программы 5S может показаться сложной задачей.Это похоже на крупную уборку в гараже или подвале дома; есть много вещей, с которыми нужно разобраться, и начало работы, вероятно, не звучит весело.
Начните с практических шагов, таких как решение, какие отделы и отдельные лица будут задействованы, какое обучение необходимо и какие инструменты использовать для облегчения процесса. Определение этих конкретных вещей поможет начать процесс внедрения 5S.
Кто должен участвовать в 5S?
Вот краткий ответ на этот вопрос: все.Если подразделение запускает 5S, необходимо включить менеджеров и всех других сотрудников. Если кто-то останется в стороне, это может привести к путанице или беспорядкам, которые люди не хотят брать на себя.
Возможно, что одни люди будут играть более важную роль в 5S, чем другие, и это нормально. Могут быть координаторы 5S, которые отвечают за установку и обслуживание маркировки 5S, отслеживание назначенных задач или знакомство с системой 5S новых сотрудников отдела. Эти люди, очевидно, будут много думать о 5S по сравнению с другими.Однако каждый должен регулярно думать о 5S. Изначально 5S может проводиться как мероприятие, но в идеале он становится частью повседневной работы для всех.
Также важно помнить, что руководители компаний должны участвовать в 5S, особенно если 5S — это усилие всей компании. Когда люди видят, что их начальство серьезно относится к 5S, участвуя в нем, они с большей вероятностью тоже отнесутся к этому серьезно.
Обучение 5S
Любой, кто будет участвовать в мероприятиях 5S, должен пройти обучение.Это можно сделать в классе, с помощью обучающего DVD и / или посредством практических занятий. Также может быть полезна демонстрация того, как 5S может возникать на рабочей станции.
Чтобы сотрудники поняли, почему компания собирается начать использовать 5S и почему это важно, им следует дать краткую историю 5S, ее составных частей и преимуществ.
Вполне возможно, что способ реализации 5S в одной организации или даже в одном отделе будет отличаться от других, поэтому группам, впервые выполняющим 5S, может потребоваться выработать наилучший способ выполнения шагов 5S в своих помещениях.
В любом случае каждый должен пройти обучение, когда 5S является новым, а затем все новые сотрудники, которые придут на работу позже, также должны пройти обучение по 5S.
5S и визуальная связь
Ключевой частью 5S является то, что он делает пространство чище и, следовательно, легче ориентироваться. Это означает, что людям будет легче выполнять свою работу. Инструменты визуальной коммуникации, такие как ярлыки, маркировка пола, маркировка шкафов и полок, а также теневые доски, могут сделать навигацию по пространству еще проще.Кроме того, эти инструменты могут помочь организовать рабочее пространство. Рабочее место, которое использует визуальное управление таким образом, часто называется визуальным рабочим местом .
Некоторые общие визуальные инструменты, используемые в 5S:
- Лента для разметки пола
- Эти ленты можно использовать для обозначения рабочих участков, отметки мест размещения оборудования или материалов или выделения опасностей. Они бывают разных цветов и узоров, а также могут использоваться на полках, верстаках, шкафах и других поверхностях.
- Этикетки и знаки
- Эти визуальные элементы используют текст, цвета и символы для передачи информации. Они могут указывать содержимое ящиков, указывать на опасности или указывать людям, где хранить детали. Существует множество стилей и размеров, и некоторые предприятия даже предпочитают изготавливать их самостоятельно с помощью принтера для этикеток и вывесок.
- Теневые доски и пена для ящиков для инструментов
- Эти визуальные эффекты полезны в рабочих областях с большим количеством инструментов. В теневых досках используются вырезы для инструментов, которые размещаются за местом, где инструмент висит на вешалке.Пена для инструментов работает аналогично, за исключением того, что она помещается в ящик для инструментов. Форма инструмента вырезана из верхнего слоя поролона, поэтому сквозь него просвечивает яркий нижний слой поролона. Оба этих метода выделяют недостающие инструменты и сообщают людям, где именно они должны быть размещены, когда они закончат их использовать.
Компании могут использовать некоторые или все эти визуальные инструменты. Все они помогают достичь часто цитируемой поговорки 5S: «Все на своем месте, и все на своих местах». Эти инструменты проясняют место вещей, поэтому беспорядок не так легко превращается в проблему.
Совет: Если вы используете разметку пола с цветовой кодировкой, ленты или другие визуальные подсказки, убедитесь, что все их понимают. При необходимости разместите таблицу цветов.
5S Внешнее производство — в здравоохранении, офисе или правительстве
5S был создан в обрабатывающей промышленности Toyota и оказался полезным для производителей во многих отраслях, не только в автомобильной промышленности. В последние десятилетия 5S вышла за рамки производства в другие отрасли, такие как здравоохранение.Во многих офисах также используется 5S, как и в некоторых школах и других государственных организациях.
Основные шаги 5S можно применить на любом рабочем месте. Офис может использовать 5S для организации поставок, так же как и больницы и медицинские клиники. 5S можно использовать даже на общей кухне, чтобы холодильник не заполнялся просроченными продуктами. На самом деле это просто вопрос определения того, какие рабочие пространства и рабочие процессы получат наибольшую выгоду от улучшенной организации рабочего места.
5S Пример
Посмотрите на пример ниже, чтобы увидеть 5S в действии.До 5S места загромождены и сбивают с толку. После 5S у всего есть назначенное место, которое часто отмечается лентой для разметки пола, этикетками и другими визуальными подсказками.
Когда 5S используется на рабочем месте, легче обнаружить отклонения и выявить потенциальные проблемы, прежде чем они перерастут в серьезные проблемы.
Стоимость 5S по сравнению с долгосрочной экономией
Руководители бизнеса, рассматривающие возможность использования 5S, могут задаться вопросом, стоит ли внедрение 5S дорого. Как правило, это не так.Могут потребоваться предварительные вложения в такие инструменты, как лента для разметки пола и этикетки, и определенное время необходимо потратить на обучение и выполнение действий 5S, которые отнимают время сотрудников. Однако в долгосрочной перспективе 5S делает процессы более плавными и предотвращает сбои, а это обычно экономит деньги предприятиям.
Что такое кайдзен (постоянное совершенствование)?
По сути означает «постоянное совершенствование», kaizen нацелено на человеческие ресурсы и процессы, чтобы закрепить отрасль для долгосрочной и успешной работы.Кайдзен — это японский термин, появившийся в период после Второй мировой войны, когда предприятия пытались справиться с последствиями войны. «Кай» переводится как «изменение», а «дзен» означает «хорошо». Кайдзен принес значительные результаты для таких компаний, как Toyota, и стал популярной производственной философией во всем мире.
В бережливом производстве кайдзен — это практика постоянного внесения небольших постепенных улучшений в более безопасное, продуктивное и эффективное рабочее место. Этот основополагающий метод бережливого производства обеспечивает непрерывное совершенствование структуры культуры вашей компании, а это означает, что менеджеры, руководители групп и работники будут постоянно искать способы улучшить процессы и ужесточить стандарты.Обзоры и обучение кайдзен учит новых сотрудников, как применять принципы кайдзен в своей работе, что означает, что кайдзен остается устойчивым на долгие годы.
Процесс постоянного улучшения на рабочем месте
Непрерывное совершенствование — это процесс постоянного улучшения вещей, чем они были раньше. Кайдзен можно определить как философию и практику постоянного улучшения. Это относится к практике поиска путей улучшения рабочих процессов на регулярной основе.Практика предполагает небольшие, постепенные изменения, а не большие изменения. С помощью кайдзен все люди в организации ищут возможности для улучшения, а не только менеджеры или руководители.
Без кайдзен
- Нет структуры в процессе улучшения; несколько процедур набора
- Цели не определены или расплывчаты / трудно измерить
- Изменения в процессы вносятся нечасто; мало размышлений об их эффективности
- Плана улучшения не существует; улучшение происходит случайно
С Кайдзен
- Идет постоянный процесс улучшения
- Процесс улучшения имеет четко определенные, измеримые цели
- Происходит постоянный анализ успехов, и оценивается сам процесс улучшения
- Последовательность процесса ведет к новым, более высоким целям
Философия кайдзен
East vs.Запад
Масааки Имаи считал, что Восток и Запад по-разному использовали концепцию непрерывного совершенствования. Имаи считал, что японцы (на востоке) использовали метод градуализма. Это то, что Имаи назвал Кайдзен . Имаи считал, что западные компании использовали методологию большого скачка вперед. Имаи назвал это нововведением. Восточная модель небольших постепенных изменений рассматривает картину в целом. Эти изменения могут показаться незначительными в момент их внедрения, но со временем они могут привести к значительным улучшениям.В этой модели упор делается на долгосрочную перспективу. Имаи считал, что восточная модель улучшения требует небольших шагов для долгосрочных, непрерывных постепенных изменений. Восток использовал всех в компании, и все вместе работали над поддержанием и улучшением. Имаи считал, что этот подход требует небольших вложений, но требует больших усилий для поддержания. Он считал, что это лучше для медленного экономического роста.
Западная модель улучшения предпочитает быстро видеть результаты. Следовательно, большие изменения, результаты которых можно увидеть быстро, как правило, претворяются в жизнь.Плюс этого метода в том, что сразу наблюдаются положительные результаты, что, как правило, радует руководителей компании и может мотивировать сотрудников. Обратной стороной является отступничество; организации, которые всегда внедряют внезапные, большие изменения, часто видят, что эти улучшения со временем исчезают.
Имаи считал, что западная модель усовершенствования сделала большие шаги для краткосрочных, прерывистых резких изменений. Запад использовал в компании несколько избранных людей, и эти люди работали над тем, чтобы сломать и восстановить. Имаи считал, что этот подход требует больших вложений, но требует небольших усилий по поддержанию.Он считал, что это лучше для быстрого экономического роста.
Кайдзен имеет тенденцию попадать в восточную модель улучшения; небольшие изменения вносятся регулярно, и со временем они могут принести бизнесу множество преимуществ. Люди могут легче выполнять задачи, чувствовать себя уполномоченными, что они могут вносить изменения сами, и находить реальные способы помочь бизнесу. Одна из причин, по которой небольшие изменения могут быть полезными, заключается в том, что они обычно не требуют больших затрат и их довольно легко реализовать. Если по какой-то причине изменение не сработает, значит, не было большого вреда, потому что на изменение изначально было потрачено мало ресурсов.
ПреимуществаКайдзен приносит пользу организациям по многим причинам. Вот некоторые из этих преимуществ:
- Более плавные и эффективные процессы
- Более чистое и безопасное рабочее место
- Продукция и / или услуги более высокого качества
- Меньшие затраты
- Повышение морального духа и вовлеченности сотрудников
- Лучшее обслуживание клиентов
Уважение к людям
В кайдзен все работники должны чувствовать себя уважаемыми, чтобы им было удобно вносить предложения по улучшению процесса.Это означает, что руководство должно верить, что работники способны вносить изменения. Люди знают свою работу лучше, чем кто-либо другой, поэтому они часто имеют представление о возможных улучшениях, которых не будет у людей, не выполняющих свою работу ежедневно. Важно отметить, что, когда людей просят искать возможные улучшения в рамках кайдзен, их не следует просить просто искать способы экономии. Некоторые улучшения могут не привести к прямой экономии затрат, но они могут сделать процесс более плавным или улучшить рабочую среду для людей, участвующих в нем.
Люди должны искать улучшения, которые улучшат их работу, и, в свою очередь, эти улучшения могут помочь компании и ее клиентам. Людей также следует поощрять к тому, чтобы они сами проверяли идеи и вносили изменения по мере необходимости. Сотрудники могут сначала проконсультироваться с коллегой или руководителем, или, если идея достаточно мала, сотрудник может пойти дальше и реализовать идею, чтобы посмотреть, как она пойдет (в зависимости от политики на рабочем месте — некоторые учреждения предпочитают, чтобы сотрудники всегда проконсультируйтесь с руководителем перед тем, как опробовать идею).В общем, рабочие места, использующие кайдзен, доверяют людям пробовать разные вещи и не всегда полагаются на руководство при принятии каждого решения.
Роль руководстваМенеджмент играет решающую роль в успехе кайдзен и должен:
- Ищу способы улучшить свою работу
- Помогите поддерживать и улучшать стандарты
- Укажите цели или задачи для улучшения
- Действия поддержки с доказательствами
Каждое рабочее место уникально, и стратегии, которые помогают улучшить одно учреждение, могут не работать в другом.Задача руководства — поддерживать людей, пока стратегии проверяются, и давать общие рекомендации относительно того, в каком направлении движется организация. При изменении стандартов руководство должно убедиться, что все осведомлены об изменениях, и убедиться, что изменения задокументированы. Всякий раз, когда руководство решает внедрить изменение, отображение данных в поддержку этого помогает облегчить поддержку со стороны других в организации, потому что люди не чувствуют, что руководство принимает решения по прихоти. Сотрудники могут видеть, что изменения вносятся целенаправленно для достижения целей организации.
Инструменты кайдзен
Кайдзен направлен на повышение эффективности и производительности, но делает это за счет создания здоровой рабочей среды для сотрудников. Это, в свою очередь, создает организованную и творческую рабочую среду, которая обогащает компанию, сотрудников и услуги, предоставляемые потребителю. Кайдзен работает по циклу, который требует сотрудничества всех отделов и может даже распространяться на поставщиков.
Цикл PDCA
Ярким примером кайдзен является реализация процесса, называемого циклом PDCA.Это метод Plan, Do, Check, Act . Первым шагом в PDCA является выполнение плана и накопление данных, которые позже будут использоваться для сравнений. Когда результаты достигнуты, они затем проверяются и сравниваются с ожидаемым результатом. Затем результаты обсуждаются и уточняются, чтобы разработать новый план. Применение нового плана — это последний шаг цикла, затем он начинается снова с тестов и сбора данных. Если процесс повторяется и данные поддаются измерению, то каждый цикл ведет к улучшению.
PDCA — это повторяющийся метод, который гарантирует, что знания о производственном процессе увеличатся, что приведет к улучшениям. Это прекрасный пример кайдзен, поскольку улучшения являются циклическими и непрерывными.
Круги качества
Эти элементы включают командную работу, самодисциплину, повышение морального духа, кружки качества и предложения. Хотя большинство этих терминов довольно прямолинейны, «кружки качества» — это новый термин для многих людей. Круги по качеству и предложения — две основные силы, стоящие за успехом Toyota с Кайдзен.
Круги — это команды, которые сосредоточены на выявлении, анализе и предложении решений рабочих проблем. Он состоит из студентов и / или рабочих с руководителем группы и способствует развитию и выражению индивидуальных идей, а не делегированию отдельных заданий. Это помогает сосредоточиться на решении проблем, а не указывать пальцем на ошибку. Японские предприятия обычно рассматривают производственную линию как уже установленный круг качества, поскольку быстрое выявление проблемы на первом этапе производства может уменьшить серьезные проблемы в дальнейшем.Каждый рабочий проходит обучение по устранению неисправностей, возникающих на их рабочем месте. Если каждая станция выполняет контроль качества, сокращение затрат и времени дает положительный эффект.
5S
Кайдзен построен на основе 5S, в первую очередь исключение отходов и стандартизация. 5S закладывает прочную основу для будущей деятельности по кайдзен. 5S устанавливает организационную систему, в которой каждый на рабочем месте участвует в устранении беспорядка и эффективном расстановке пространств.Пока пространство очищается и организовывается с помощью 5S, менеджеры должны поощрять операторов и рядовых работников вносить предложения по улучшению. Такая система упрощает людям поиск возможностей для улучшения, скрывающихся у всех на виду, а также способствует командной работе и самодисциплине.
Кайдзен События
Хотя многие компании предпочитают практиковать философию Кайдзен в своей повседневной деятельности, мероприятия Кайдзен могут пригодиться для более крупных проектов. Событие кайдзен (также известное как блиц кайдзен) — это запланированный процесс улучшения, который происходит в течение нескольких часов, дней или даже может растянуться на пару недель.Создана команда мероприятия, которой определен фокус.
Кайдзен-события используются разными способами, включая изменения процесса, изменения планировки на предприятии, устранение отходов и стандартизацию. Окончательное определение масштаба мероприятия кайдзен — ключ к успеху блица. Проекты улучшения часто начинаются с разумного объема, но сверхурочные работы становятся слишком большими и неуправляемыми. На этапе планирования команде кайдзен необходимо будет выбрать область или процесс для улучшения и определить масштаб мероприятия.
Кайдзен и постоянное совершенствование
Мышление кайдзен о постоянном совершенствовании делает рабочее место более продуктивным и эффективным за счет внесения небольших изменений и акцентирования внимания на вовлечении всех сотрудников. Кайдзен устанавливает последовательный процесс улучшения, определяет цели организации и дает менеджерам инструменты, необходимые для достижения этих целей.
Информация о 6S — система 6s
Чем 6S отличается от 5S?
6S — это, по сути, система 5S, с добавленной шестой и очень важной буквой S: БЕЗОПАСНОСТЬ!
По нашему Что такое 5S? странице, мы узнаем, что первые 5S обозначают:
- Сортировка (Seiri) — Удалите все неиспользуемые в рабочем пространстве вещи и храните их.
- Упорядочить (Seiton) — Расположите предметы, используемые ежедневно, так, чтобы к ним можно было легко получить доступ и быстро хранить.
- Shine (Seiso) — Все очищено и работает исправно.
- Стандартизация (Seiketsu) — Разработайте процедуру сортировки, закрепки и сияния.
- Sustain (Shitsuke) — Создайте культуру, которая ежедневно следует шагам.
Теперь для 6S добавляем:
- Безопасность — Убедитесь, что безопасность стоит во главу угла при каждом процессе и предпринимаемых действиях.
Безопасность
Мы все знаем, что такое безопасность, но как сделать вашу рабочую среду более безопасной? OSHA и ANSI установили определенные стандарты, которые повышают безопасность, но есть еще кое-что, что можно сделать, помимо простого соблюдения «стандартов».
5S основан на концепции визуального рабочего места.
Чтобы обеспечить безопасность вашего объекта, склада или офиса, вам необходимо визуально отмечать все опасности, оставаться организованным и после использования возвращать инструменты и оборудование на их место.Чтобы убедиться, что все сотрудники работают, чтобы поддерживать эту организацию, визуальные подсказки являются ключевыми.
Разметка полов
Напольную лентуможно использовать для маркировки проходов, складских площадок для поддонов и стеллажных систем. Напольные знаки могут быть невероятно полезны для предоставления информации рабочим, например, где есть движение вилочных погрузчиков, где расположена станция для промывки глаз, где поставить мусорный бак (чтобы он всегда оставался на одном месте или где припарковать домкрат для поддонов. Вся эта разметка пола помогает обезопасить ваше рабочее место.
Маркировка
Маркировка — еще один способ сохранить рабочее место организованным и безопасным. Маркируете ли вы трубы или маркируете складские стеллажи, системы хранения или опасные материалы, этикетки являются ключом к 6S. У сотрудников гораздо меньше шансов получить травмы, если предметы правильно поставить на место, не говоря уже о том, что они будут намного эффективнее работать в организованной среде. Пакет этикеток 5S — это экономичный метод создания визуального рабочего места.
Средства общей безопасности
Не забудьте про предметы первой необходимости для обеспечения безопасности 6S, такие как каски и защитные очки.Сделайте безопасность частью своей рабочей культуры, и вы увидите результаты.
Нет причин ждать. Начните работу по программе 6S сегодня!
Краткое руководство по организации рабочего места 5S
Методика организации рабочего места 5S — это распространенная методология, которую компании могут использовать для улучшения своей деятельности. Цель состоит в том, чтобы повысить эффективность, минимизировать отходы и в целом оптимизировать работу. Техника 5S чаще всего используется в производственных и складских организациях, но она может принести значительную пользу практически в любой отрасли.Изучение принципов 5S поможет вашей организации получить ее преимущества и успешно реализовать ее.
5 S
5S может показаться странным названием для стратегии организации рабочего места, но это имя имеет значение. Это связано с тем, что существует пять областей, в которых можно улучшить рабочую среду. Эта техника зародилась в Японии, поэтому пяти категориям изначально были даны японские имена, каждая из которых начиналась с буквы S.Они были переведены на английский язык, также с названиями буквой S для единообразия.
Пять S:
- Сортировка — Все, что не требуется для выполнения оперативных задач, следует убрать с территории. Удаление ненужных предметов помогает устранить беспорядок и упростить доступ ко всему необходимому.
- Set — Установка порядка означает обеспечение того, чтобы каждый элемент на рабочем месте имел определенное место, где он хранится.Это сводит к минимуму риск потери или потери чего-либо и гарантирует, что вещи не будут повреждены из-за неправильного хранения.
- Shine — Поддержание оборудования, инструментов и оборудования в хорошем рабочем состоянии устраняет многие потенциальные проблемы. Задачи, связанные с блеском, включают регулярное обслуживание, чистку и ремонт предметов, которые требуют внимания.
- Стандартизация — Каждое рабочее место должно иметь стандарты, которым все должны следовать. Стандартизация включает определение прав собственности на различные активы и задачи, чтобы сделать рабочую среду предсказуемой.
- Sustain — Поддержание организации рабочего места — самый сложный шаг из всех, поэтому он получает свою собственную категорию. Об устойчивом улучшении не следует думать второстепенно. Должен быть план пересмотра каждого из четырех других пунктов и лицо (или люди), которые несут ответственность.
В дополнение к этим пяти категориям некоторые организации включают «Безопасность» и считают ее шестой S. Когда она включена, система иногда называется 6S или 5S + Safety.А остальные 5 — это то, что вы делаете. Безопасность — это то, чего можно достичь, если они хорошо выполнены.
Контрольные списки 5S
Как мы уже упоминали, поддержание методологии 5S может быть проблемой. Знать концепции, лежащие в основе каждой из S, необходимо, но для их практического применения требуются определенные усилия. Контрольные списки 5S — отличный инструмент для поиска вещей, которые не соответствуют 5S, и их исправления. Контрольный список 5S также является полезным инструментом для аудита предприятия и внесения улучшений там, где это необходимо.
Менеджеры или операторы могут взять контрольный список, включающий различные элементы 5S, и отправиться в Гемба (место, где выполняется работа). Они могут идентифицировать все, что несовместимо с 5S, и задокументировать это, чтобы потом исправить или улучшить. При выполнении анализа 5S полезно внимательно следить за каждым этапом каждого процесса и задачи, чтобы убедиться, что все возможности для улучшения определены. Если делать это регулярно, это будет способствовать постоянному совершенствованию и будет способствовать сохранению достигнутых успехов.
Преимущества внедрения 5S
Внедрение 5S требует усилий и ресурсов, поэтому очень важно понимать, какие преимущества вы получите. Многие преимущества, такие как меньшее количество дефектов, меньшие затраты на техническое обслуживание и ремонт, а также более приятное место для работы, очевидны, но некоторые из них являются неожиданными.
Например, организация, использующая методологию 5S, обнаружит, что их производительность может значительно возрасти. Такая повышенная эффективность стала возможной благодаря тому, что многие препятствия, замедляющие работу людей и систем, были устранены или смягчены, чтобы обеспечить более плавное выполнение операций.
Сокращение отходов — еще одно важное преимущество. За счет улучшения операций сокращается количество дефектов и повышается эффективность использования всех ресурсов. Наконец, одним из часто упускаемых из виду преимуществ 5S является повышение вовлеченности и удовлетворенности сотрудников. 5S дает сотрудникам возможность улучшать свое рабочее пространство, что приносит пользу компании и позволяет сотрудникам выполнять свою работу наилучшим образом.
Внедрение 5S — разумный шаг для любой компании, стремящейся улучшить производственные процессы.Его легко и недорого внедрить, и если он будет поддерживаться в течение длительного времени, он может обеспечить компании получение преимуществ, которые со временем будут расти.
Что такое система 5s? | Определения, основные концепции и принципы
Что такое система 5S?
Система 5S — это инструмент бережливого производства, повышающий эффективность рабочего места и устраняющий отходы. В системе пять шагов, каждый из которых начинается с буквы S:
.Предоставляя систематическую основу для организации и чистоты, 5S помогает предприятиям избежать потери производительности из-за отложенной работы или незапланированных простоев.
Шаги 5S
5S был создан в Японии, и исходные термины «S» были на японском языке, поэтому английский перевод для каждого из пяти шагов может отличаться. Однако основные идеи и связи между ними легко понять.
Имя шага | Японский термин | Пояснение |
---|---|---|
1. Сортировать | Сейри (опрятность) | Удалите ненужные предметы из каждой области |
2.Установить в заказ | Сейтон (упорядоченность) | Организуйте и определите хранилище для эффективного использования |
3. Блеск | Seiso (чистота) | Регулярно очищайте и осматривайте каждую зону |
4. Стандартизация | Seiketsu (стандартизация) | Включение 5S в стандартные рабочие процедуры |
5. Сустейн | Сицукэ (дисциплина) | Назначьте ответственность, отслеживайте прогресс и продолжайте цикл |
Эти шаги взаимосвязаны, поэтому последовательность важна.
Удаление ненужных материалов на шаге 1 (Сортировка) предоставит пространство, необходимое для организации важных элементов на шаге 2 (Установить по порядку).
Затем, как только рабочее пространство будет расчищено и организовано, грязь и сажа можно удалить на шаге 3 (Полировка).
Эти изменения в должностных обязанностях работников и рабочей среде должны быть отражены в обновленных процедурах на этапе 4 (Стандартизация).
Наконец, эти новые процедуры мало что значат, если не будут возложены ответственность и не будет отслеживаться прогресс — как это требуется для шага 5 («Поддержание»).И с ответственностью и отслеживанием работники будут продолжать применять шаги, возвращаясь к шагу 1.
Шаг 1. Сортировка
Первым шагом в процессе 5S является сортировка, или seiri, что переводится как «аккуратность». Цель этапа сортировки — устранить беспорядок и расчистить место, удалив вещи, которые не принадлежат этой области.
Очистка рабочей области
На этом этапе внимательно посмотрите на предметы, инструменты и материалы в рабочей области. Там должны храниться предметы, которые необходимы или полезны для работы, выполняемой в этом месте.Все остальное нужно удалить.
Некоторые из этих удаленных предметов необходимо выбросить или переработать. Другие элементы могут принадлежать другому рабочему процессу или месту; они должны быть возвращены в их «дома». Однако вы можете найти некоторые элементы, в которых не уверены.
Неизвестные предметы с красной пометкой
Если вы обнаружите предмет, который не можете идентифицировать или у которого нет уверенности в праве собственности, пора использовать красный ярлык. «Red-Tagging» временно прикрепляет к элементу хорошо заметный тег, в котором отмечается, где и когда он был найден.Затем отмеченные красными метками предметы со всех рабочих зон собираются в одном месте: «потерянное и найденное» для инструментов, материалов и оборудования.
Если в рабочей области отсутствует важный инструмент, проверьте область сбора красных тегов, чтобы увидеть, не был ли он найден где-то еще. Руководители каждого рабочего места должны периодически проверять область сбора красных ярлыков на случай, если что-то было упущено. Все, что принадлежит рабочему пространству, следует вернуть туда.
Переназначение элементов с тегами
Предметы могут долго ждать в зоне сбора красных меток.В этом случае исходная рабочая область (откуда этот элемент), похоже, больше не нужна. Тем не менее, это может быть полезно в другом месте.
В одном из распространенных подходов предметы могут оставаться в зоне сбора красных ярлыков в течение тридцати дней. После этого любой руководитель может потребовать предмет для своего рабочего места. Если через неделю он никому не понадобится, его можно полностью вывезти из учреждения. Продайте, утилизируйте или выбросьте.
Если товар определенно понадобится компании, но в данный момент он не нужен, возможно, лучше оставить его на потом.Прежде чем положить что-либо на хранение, убедитесь, что это действительно понадобится снова. Составьте конкретный план, как снова вытащить этот предмет из хранилища в определенное время. Не храните вещи «на всякий случай» без уважительной причины и следите за тем, что было сохранено.
Шаг 2: Установить порядок
Второй шаг, «Установить порядок», изначально назывался «сейтон», что переводится как «упорядоченность». В английском языке используются различные названия: «Систематическая организация», «Выравнивание» и «Упростить», например.Независимо от того, как он называется, цель этого шага — организовать рабочую зону. Каждый предмет должен быть легким для поиска, использования и возврата: для всего должно быть место, и все на своем месте.
Создание карты 5S
Часто используемые инструменты следует хранить рядом с местом их использования. Запасное оборудование, расходные материалы и другие инструменты, которые используются реже, можно хранить в центральном месте, где несколько команд могут ими пользоваться. Предметы, которые обычно используются вместе (например, сверла и сверла), следует хранить рядом друг с другом.Каждое из этих решений будет иметь смысл само по себе, но может стать трудно отслеживать все. В рамках этого процесса может оказаться полезным создание карты 5S.
Карта 5S — это диаграмма или план этажа, который обеспечивает обзор рабочей зоны, процесса или станции. Он предоставляет визуальную ссылку, чтобы показать, где находятся инструменты, расходные материалы, рабочие и пути передвижения, и как они соотносятся друг с другом. Хорошая карта может также включать описание работ, которые происходят в указанной области.
В зависимости от потребностей вашего учреждения один подход может оказаться для вас проще, чем другой:
- Составьте карту, а затем реализуйте ее
- Сначала физически расположите рабочее место, а затем нанесите его на карту
- Составьте карту на ходу, тестируйте идеи и записывайте, что хорошо работает
Независимо от того, какой подход используется для ее создания, полученную карту 5S следует сохранить в качестве обучающего инструмента, использовать для справки на более поздних этапах 5S и обновлять с течением времени по мере изменения рабочей области.
Сообщение плана
После назначения мест хранения необходимо пометить каждую область хранения. Маркируйте дверцы шкафа снаружи, чтобы работники могли быстро определить, что внутри каждой из них. Затем пометьте все внутренние полки, чтобы показать, где находятся различные принадлежности. Те же идеи распространяются на этикетки для стоек, ящики и другие системы хранения.
Многие предприятия используют «теневую доску» для хранения инструментов, чтобы каждый инструмент можно было легко вернуть на место для хранения.При таком подходе метка, соответствующая форме и размеру инструмента, размещается там, где ему принадлежит. Рабочие могут сразу определить, где находится каждый предмет, и сразу узнать, есть он там или нет. Больше не нужно тратить время на просмотр ящиков и корзин.
Организация может распространяться и на этаж. Рабочие зоны, передвижные полосы и склады для расходных материалов и готовой продукции могут быть отмечены лентой для разметки пола.
Шаг 3: Сияние
Третья ступень 5S — это сияние, или «сейсо», что означает «чистота».«В то время как первая и вторая ступени расчистили пространство и организовали зону для повышения эффективности, на этом этапе удаляется грязь и сажа, которые неизбежно накапливаются под беспорядком, и предотвращается его повторное появление.
Регулярная чистка
Shine выходит далеко за рамки того, чтобы просто время от времени толкать метлу. Он включает в себя регулярную уборку каждой части рабочей зоны — часто ежедневную уборку и более тщательную уборку каждую неделю.
Важно отметить, что ступенька Shine не предназначена для обслуживающего или уборочного персонала.Каждый рабочий должен убирать свое рабочее место и оборудование, которое он использует. Этот подход имеет несколько преимуществ:
- Рабочие, знакомые с местностью, быстро заметят любые возникающие проблемы.
- Опасности или сложные ситуации будут поняты и учтены
- Объекты, которые не на своем месте или отсутствуют, будут признаны
- Рабочие стараются содержать свое рабочее место в чистоте во время обычных операций
Каждый должен обращать внимание на общую чистоту на рабочем месте, быть готовым убирать мусор и так далее.Но для того, чтобы 5S давала наилучшие результаты, каждый работник должен нести личную ответственность за свое рабочее пространство.
Сияние как профилактическое обслуживание
Содержание в чистоте на рабочем месте дает много преимуществ. Одним из важных преимуществ является то, что легко обнаружить утечки, трещины или перекосы. Если люди, поддерживающие чистоту в помещении, — это те же люди, которые там работают регулярно, они быстро распознают любую из этих проблем.
Если оставить эти проблемы незамеченными и нерешенными, это может привести к отказу оборудования, угрозе безопасности и снижению производительности.Благодаря постоянной очистке и осмотрам, используемым на этапе «Сияние» 5S, система может быть включена в программу профилактического обслуживания. Таким образом, 5S может продлить срок службы оборудования и сократить время простоя в аварийных ситуациях.
Шаг 4. Стандартизация
Первые три шага 5S охватывают основы очистки, организации и очистки рабочего пространства; сами по себе эти шаги принесут краткосрочные выгоды. Четвертый шаг — это стандартизация, или «сэйкэцу», что просто означает стандартизация.Записывая, что делается, где и кем, вы можете включить новые практики в обычную рабочую процедуру. Это открывает путь к долгосрочным изменениям.
Сила записывать
Говорят: «Если это не записано, этого не произошло». Запись решений, которые вы принимаете в программе 5S, поможет гарантировать, что ваша работа не исчезнет просто так. Если вы создали карту 5S на этапе «Установить в порядке», эта карта может стать частью вашего нового стандарта для данной области.Таким же образом можно записать и включить в стандарты процесс, который вы используете для красной маркировки элементов.
Впрочем, если вы записываете свои решения, это не значит, что вы не можете их изменить. Цель 5S — улучшить ваше рабочее место, а не сделать его неизменным. Вы пишете стандарты для своего учреждения и можете изменить их, чтобы они соответствовали новой информации или новым потребностям бизнеса.
Инструменты для стандартизации
После того, как вы приняли решение о том, как изменить свои методы работы, эти решения необходимо сообщить работникам.Это общение — ключевая часть этапа стандартизации. Общие инструменты для этого процесса включают:
- Контрольные списки 5S — Перечисление отдельных этапов процесса позволяет работникам полностью следовать этому процессу. Он также предоставляет простой инструмент аудита для проверки прогресса позже.
- Диаграммы цикла заданий — Определите каждую задачу, которая должна быть выполнена в рабочей области, и выберите график или частоту для каждой из этих задач. Затем возложите ответственность на конкретного работника (или должностную обязанность).Полученную диаграмму можно разместить на видном месте для решения вопросов и повышения ответственности.
- Таблички и знаки с инструкциями — Предоставьте инструкции по эксплуатации, действиям по очистке и профилактическому обслуживанию там, где эта информация будет необходима.
Шаг 5: Сустейн
Пятый шаг программы 5S — Sustain, или «сицукэ», что буквально означает «дисциплина». Идея здесь — постоянная приверженность. Важно выполнять принятые вами решения и постоянно возвращаться к предыдущим шагам 5S в непрерывном цикле.
Никогда не «однажды и сделано»
Подход 5S никогда не задумывался как разовое мероприятие, а должен был стать непрерывным циклом. Это ключевой момент, потому что первые успехи в 5S могут открыть путь для проблем. Если открытое пространство становится доступным на этапе сортировки, но после этого инструментам и материалам разрешается постепенно заполнять это пространство без какой-либо организации, в конечном результате может возникнуть еще больший беспорядок. Решение состоит в том, чтобы применять идеи 5S снова и снова, как рутинную часть нормальной работы. Вот почему так важен сустейн.
Поддержка программы 5S может означать разные вещи на разных рабочих местах, но есть некоторые элементы, которые являются общими для успешных программ.
| |
| |
| |
| |
|
Сустейн — это не конец 5S
Хотя это последний шаг в последовательности, сустейн не является концом 5S в целом. Один проход по этапам может выявить проблемы, которые были скрыты заранее. Повторное выполнение этих шагов может решить эти проблемы и помочь найти новые способы улучшения. Продолжайте цикл снова и снова, чтобы ваше предприятие было максимально эффективным.
Шестая буква «S» для безопасности
Когда дело доходит до бережливого производства и улучшения рабочих мест, 5S является одним из наиболее широко известных и используемых инструментов бережливого производства. Это неудивительно: 5S может повысить эффективность рабочего места, снизить затраты и улучшить качество. Но со многими программами бережливого производства легко сосредоточиться только на этих целях и упустить из виду человеческий фактор. Безопасность работников имеет решающее значение. Вот почему многие предприятия добавляют еще одну ступень к циклу 5S, называя результат «6S» — с безопасностью.
В отличие от первых пяти шагов, безопасность не является последовательным шагом. Это необходимо учитывать на всех остальных этапах. Например, на этапе сортировки вы можете решить, что данный инструмент устарел, потому что более новая версия более безопасна в использовании. Аналогичным образом, на этапе стандартизации рабочие процедуры должны быть стандартизированы для повышения безопасности на рабочем месте, а не только эффективности.
Обеспечение безопасности рабочих — это не просто дело: случайные травмы на рабочем месте обходятся дорого.Исследование Стэнфордского университета показало, что затраты на перелом костей могут стоить компании 50 000 долларов авансом, а также еще 55 000 долларов в виде косвенных затрат. Каждый инцидент может привести к проверке и цитированию OSHA, а также к увеличению затрат на страхование.
(Источник: РЕАЛЬНАЯ стоимость требования компенсации рабочим, Джефф Кавиньяк)
Выбор внедрения 6S вместо стандартной программы 5S может помочь вам улучшить организацию и эффективность рабочего места, а также сделать рабочее место более безопасным.
Преимущества программы 5S
Поскольку 5S ориентирована на улучшение рабочего места, а разные рабочие места могут иметь мало общего, может быть трудно предсказать точные результаты использования программы. Однако почти всегда можно найти некоторые преимущества:
| |
| |
| |
| |
| |
|
Эти преимущества — не просто хорошие чувства.Документируя свое положение до и после внедрения 5S, многие предприятия смогли продемонстрировать реальные измеряемые улучшения.
Например, Университет Джорджии запустил программу бережливого производства в 2009 году. Используя 5S, они сократили расстояние перемещения для обработки материалов на 83%, экономя от 7 000 до 10 000 долларов США на рабочей силе каждый год. (Источник: http://www.busfin.uga.edu/ )
Точно так же в больнице использовались принципы 5S, чтобы сократить время настройки в операционных на 37%, а количество инструментов, необходимых для некоторых процедур, сократилось на 70%.С финансовой точки зрения больница сэкономила около 2,8 миллиона долларов в год. (Источник: Journal for Healthcare Quality. Сентябрь / октябрь 2015 г., том 37, выпуск 5)
5S в бережливом производстве
Бережливое производство — это образ мыслей о продуктивных системах с упором на сокращение ненужного, то есть на сокращение напрасных материалов, усилий и времени.Такой подход помогает повысить общую производительность, качество и прибыль. 5S естественно подходит здесь, потому что он способствует упрощению, организации и чистоте рабочего места.
Некоторые другие инструменты под эгидой бережливого производства особенно хорошо работают в сотрудничестве с 5S. Например:
- Кайдзен — Внесите множество небольших изменений в стремлении к постоянному совершенствованию. Совокупные результаты могут привести к значительному повышению качества, безопасности и прибыли. Постоянный цикл улучшений идеально соответствует шагу Sustain 5S.
- Канбан — используйте управляемую спросом производственную цепочку, чтобы переориентировать внимание на потребности клиентов и сократить ненужные запасы поставок, запасы и незавершенное производство. Подобная оптимизация рабочих процессов, по сути, применяет этап сортировки 5S ко всему бизнесу, а не только к рабочей области.
- Total Productive Maintenance — Профилактическое обслуживание и автономное обслуживание для повышения продуктивности использования всего оборудования. Сокращение времени простоя и устранение ошибок приведет к повышению производительности и прибыльности.Шаг 5S Shine может сыграть ключевую роль.
Следующие шаги с 5S
Чтобы узнать, как реализовать программу 5S на вашем предприятии, прочитайте нашу подробную статью о начале работы с 5S. Вы также можете запросить наше бесплатное руководство по передовой практике для системы 5S для получения пошагового подхода или в качестве полезного учебного пособия.
В процессе внедрения 5S вы обнаружите, что визуальные сигналы могут быть важной частью системы:
- Разметка пола и большие знаки показывают, где нужно собирать предметы с красными бирками
- Доски Shadow и системы маркировки демонстрируют новую систему хранения инструментов
- На этикетках с инструкциями перечислены этапы нового рабочего процесса для удобства использования
Если вам нужно создать индивидуальные визуальные сигналы для вашего предприятия, положитесь на линейку промышленных принтеров этикеток и вывесок DuraLabel, а также на линию маркировочных лент и лент безопасности PathFinder.Эти продукты предназначены для изготовления долговечных индивидуальных вывесок и маркировок для различных промышленных нужд, и они идеально подходят для реализации 5S.
Готовы начать работу с 5s на вашем предприятии?
Прочтите нашу статью «Начало работы», чтобы получить исчерпывающие инструкции по внедрению 5s.
5S — каковы пять «S» бережливого производства?
Глоссарий качества Определение: пять S (5S)
5S определяется как методология, результатом которой является чистое, незагроможденное, безопасное и хорошо организованное рабочее место, помогающее сократить отходы и оптимизировать производительность.Он разработан, чтобы помочь создать качественную рабочую среду, как физически, так и морально. Философия 5S применима в любой рабочей области, подходящей для визуального контроля и бережливого производства. Состояние 5S на рабочем месте имеет решающее значение для сотрудников и является основой первых впечатлений клиентов.
Инструмент качества 5S образован от пяти японских терминов, начинающихся с буквы «S», используемых для создания рабочего места, подходящего для визуального контроля и бережливого производства. Основы 5S просты в освоении и важны для реализации:
- Seiri: Для отделения необходимых инструментов, деталей и инструкций от ненужных материалов и удаления ненужных.
- Seiton: Для аккуратного размещения и идентификации деталей и инструментов для простоты использования.
- Seiso: Провести зачистку.
- Seiketsu: Ежедневно проводить seiri , seiton и seiso для поддержания рабочего места в идеальном состоянии.
- Сицукэ: Чтобы сформировать привычку всегда следовать первым четырем S.
Ниже японские термины переведены на англоязычную версию 5S.
Японский | Переведено | Английский | Определение |
Сейри | организовать | сорт | Удалите все ненужное, отделив необходимые инструменты, детали и инструкции от ненужных материалов. |
Сейтон | упорядоченность | комплект под заказ | Организуйте все, что осталось, аккуратно расположив и обозначив детали и инструменты для простоты использования. |
Seiso | чистота | блеск | Очистите рабочую зону, проведя кампанию по уборке. |
Seiketsu | стандартизировать | стандартизировать | Запланируйте регулярную очистку и техническое обслуживание, ежедневно проводя seiri , seiton и seiso . |
Сицукэ | дисциплина | сустейн | Сделайте 5S своим образом жизни, сформировав привычку всегда следовать первым четырем S. |
Преимущества внедрения программы бережливого производства 5S включают:
- Повышенная безопасность
- Повышенная доступность оборудования
- Меньшее количество дефектов
- Сниженные затраты
- Повышенная маневренность и гибкость производства
- Повышение морального духа сотрудников
- Лучшее использование активов
- Повышение имиджа предприятия для клиентов, поставщиков, сотрудников и руководства
Five S (5S) Пример: контрольный список диагностики сканирования на рабочем месте
5S, пример
Во время встреч с внутренними и внешними заинтересованными сторонами группа проекта по регистрации в программе Medicaid Kaiser Permanente Colorado использовала инструмент бережливого 5S для улучшения шаблона регистрации, а также процесса шаблонов.Они реализовали столпы 5S следующим образом:
- Поля были отсортированы , и ненужные поля удалены.
- Поля были установлены в порядок на основе ввода заинтересованных сторон.
- Команда осветила , создав базу данных Microsoft Access, которая не допускала дублирования записей.
- Электронная таблица была стандартизирована , защищая ее и сделав ее шаблоном.
- Самоподдерживающаяся система была создана с использованием Microsoft Access (для управления форматом данных и дублированием) и шаблонов Microsoft Excel (для управления форматом и порядком электронных таблиц).
Прочтите полный пример исследования: Оптимизированная сеть регистрации дает большие результаты для лидера здравоохранения (PDF)
Вы также можете искать статьи, тематические исследования и публикации по ресурсам 5S.
Книги
5S для сервисных организаций и офисов
Бережливые больницы
Статьи
Все — 5S: простой, но эффективный подход к рациональному использованию средств, применяемый в центре предварительного тестирования ( Журнал управления качеством, ) Центр предварительного тестирования применил 5S к процессу потока пациентов, оптимизируя этапы и устраняя потери.Результаты показывают, что структура 5S является эффективной и простой моделью для разработки и улучшения процессов.
Office Efficiency ( Quality Progress ) Метод бережливого производства 5S часто используется в производстве, но его можно адаптировать к офисным условиям для повышения эффективности информационных рабочих процессов. В частности, лучшая организация и управление информационными потоками позволяет работникам умственного труда принимать более обоснованные решения о расстановке приоритетов и выполнении задач.
Видео
Использование 5S в повседневной жизни Член ASQ Александр Такер, химик из Capsugel, использовал инструмент 5S в своей домашней жизни.Вы не перестанете улыбаться, когда он с юмором рассказывает о том, как он организовал свою ванную комнату, запланировал походы в продуктовый магазин и даже научил свою собаку быть качественной собакой.
Адаптировано из Основы качества: Справочное руководство от А до Я , ASQ Quality Press.
Как внедрить Lean 5S Visual Workplace Organization?
Lean 5S Visual Workplace Organization — это методология организации рабочего места, направленная на повышение производительности за счет устранения потерь и качества за счет уменьшения отклонений.
Методология 5S Visual Workplace Organization также способствует структурированному диалогу о стандартизации, который создает между сотрудниками четкое понимание того, как должна выполняться работа. Этот структурированный подход может использоваться в производственной, дистрибьюторской или офисной среде и во всех отраслях промышленности.
Визуальная организация рабочего места5S часто является первым шагом на пути к реализации инициативы Operational Excellence, основанной на бережливом производстве, поскольку она сокращает потери из-за внутренней транспортировки, движения и ожидания и создает прочную основу для внедрения потокового производства, визуального управления и стандартов. операции.
5S происходит от пяти японских слов: Seiri, Seiton, Seiso, Seiketsu и Shitsuke. Обычно переводится как «Сортировка», «Упорядочить» или «Упростить доступ», «Осветить», «Стандартизировать» и «Поддержать».
Некоторые критических факторов успеха для эффективной реализации 5S Visual Workplace Organization:
- Есть план !!!
- Лидерство — Управляйте им сверху и Идите к разговору
- Вовлечение сотрудников — Создайте группы действий 5S, и каждая смена должна заканчивать свой день хозяйственной деятельностью на территории
- Фокус — создание приоритетных областей 5S с участием сотрудников
- No Sacred Cows — 5s — это не только производственный цех.Включая склады, подсобные помещения, офисный стол,…
- Organize & Beautify — Paint — недорогой и отличный инструмент для поддержки внедрения 5S.
- Подотчетность — Обеспечьте подотчетность команд в соответствии с требованиями области
- Оценивайте и улучшайте — проводите еженедельные аудиты с руководителями групп 5S в каждой области. Публикуйте оценки.
- Сделайте это весело и Отметьте прогресс
Хотя реализация инициативы 5S Visual Workplace должна быть адаптирована к конкретным целям, требованиям и обстоятельствам организации, большинство внедрений следует за шестиступенчатым процессом.
Шаг 1. Создание организации по внедрению 5S
Группа внедрения 5S Обучение , стандартизация 5S, руководство по методам 5S и предоставление инструментов 5S. Основная цель кампании 5S — не столько объявить о начале кампании 5S, сколько показать энтузиазм и приверженность лидера 5S.
5S Leader возглавляет группу внедрения 5S.
Аудиторская группа 5S еженедельно проводит инспекционные поездки для проверки условий 5S, а также предложения и документирования мер по исправлению положения, когда условия начали ухудшаться.
Группа действий 5S , состоящая из руководителей мастерских и рядовых сотрудников, отвечает за внедрение 5S. Члены команды изучают теорию 5S, применяя ее на практике, внося улучшения, ориентированные на 5S.
Шаг 2 — Составьте план внедрения 5S
Основная цель кампании 5S — не столько объявить о начале кампании 5S, сколько показать энтузиазм и приверженность лидеров 5S.Лидеры 5S должны учитывать текущие условия организации, ее цели и план использования инициативы 5S, чтобы заложить основу для достижения этих целей. План внедрения 5S должен охватывать 90 дней за раз.
Шаг 3. Создание материала кампании 5S
Материалы кампании 5S могут включать личные встречи, информационные бюллетени, слоганы, доски, плакаты, баннеры, значки, новости 5S, фотовыставки до и после,….
Шаг 4 — Внутреннее обучение
Учебные материалы по 5S могут включать учебные классы, уроки 5S по отдельности, обучение на рабочем месте, плакаты, внутренние бюллетени, новости 5S, видео, книги и т. Д.
- Сделать образование непрерывным
- Не будь перфекционистом, но стремись к совершенству
- Первичное место для внедрения 5S — индивидуальное рабочее место
- Поощрять независимое мышление
- Поощрять мотивацию, развитие навыков и участие
- Сделайте его актуальным, конкретным и интересным
Шаг 5.1 — Сортировка (Seiri)
Сортировка — это первый шаг в процессе 5S, который включает в себя тщательное изучение всего в рабочей среде.Все импровизированные материалы или что-либо, не имеющее отношения к рабочему месту, удаляются с территории. Удаляя беспорядок и ненужный мусор, 5S устраняет опасности в рабочем пространстве. Отделение часто используемых инструментов от редко используемых элементов упрощает работу, создавая более быстрые, компактные и безопасные условия труда.
Шаг 5.2 — Упорядочение, выпрямление или упрощение доступа (Seiton)
Set-in-Order, второй шаг в процессе 5S, заключается в размещении всего в назначенной области, чтобы ее можно было использовать и вернуть как можно быстрее и безопаснее.Часто используемые инструменты должны быть легко доступны, что экономит время и силы.
Шаг 5.3 — Блеск (Seiso)
Shine, третий этап процесса 5S, фокусируется на чистоте рабочей среды для создания чистого и аккуратного рабочего пространства. Техническое обслуживание и чистота становятся частью повседневной работы, повышая безопасность рабочего места и увеличивая срок службы инструментов и оборудования. Shine фокусируется не просто на однократной очистке рабочей среды, а на ежедневном поддержании ее в чистоте, чтобы поддерживать помещение и оборудование в долгосрочной перспективе.
Шаг 5.4 — Стандартизация (Seiketsu)
После внедрения первых 3S, стандартизация, четвертый шаг в процессе 5S, создает последовательный подход к выполнению задач и процедур. Обязанности, связанные с 5S, 5-минутные периоды 5S, диаграммы циклов, визуальные подсказки и контрольные списки интегрированы в обычные рабочие обязанности, чтобы поддерживать улучшения, достигнутые с помощью первых 3S.
Шаг 6 — Сустейн (Сицукэ)
Sustain, последний и часто самый сложный шаг в процессе 5S, гарантирует, что подход 5S укоренится в организации и станет жизненно важной частью инициативы организации по повышению эффективности работы.Внедрение чемпионов и координаторов 5S, командный аудит и активное участие в текущем мероприятии по организации рабочего места 5S Visual Kaizen необходимо для изменения укоренившегося поведения и определения нового статус-кво.
Чтобы узнать больше о нашей 5S Visual Workplace Organization и других решениях для бережливого управления, посетите наши семинары или свяжитесь с нами. Посетите нашу Академию OpEx, чтобы получить загружаемые учебные материалы, модули электронного обучения, онлайн-курсы и публичные семинары.
Воспользуйтесь нашими знаниями и опытом, чтобы помочь организациям повысить прибыльность и обеспечить рост за счет совершенства операций и бережливого производства и шести сигм. Свяжитесь с нами, чтобы обсудить, как консалтинг по операционному совершенству может поддержать вас и вашу организацию в создании или ускорении вашей собственной инициативы по совершенствованию операционной деятельности. Следуйте за нами в LinkedIn и Facebook.
Опыт.